Motion controller is a core component in modern industrial automation and robotics technology, responsible for precise control and scheduling of mechanical systems. There are various forms of control for motion controllers, each with its specific application scenarios and advantages. The following is an analysis of the control form of the motion controller.
1、 Open-loop control
Open loop control is a fundamental form of control, whose core idea is for the controller to directly output control variables based on input signals, without providing feedback on the system’s output. Open loop control has the advantages of simple structure and low cost, but it also has disadvantages such as low control accuracy and poor anti-interference ability.
Pulse control: Pulse control is a common open-loop control method that controls the motion of a motor by sending pulse signals to it. Pulse control has the characteristics of fast response speed and high control accuracy, and is widely used in fields such as CNC machine tools and robots.
Simulation control: Simulation control controls the speed and direction of the motor through analog signals. Simulation control has the advantages of high control accuracy and strong anti-interference ability, but it also has problems such as limited signal transmission distance and susceptibility to electromagnetic interference.
2、 Closed-loop control
Closed loop control is a more advanced form of control, whose core idea is to introduce a feedback loop in the control process and adjust the control quantity based on the deviation between the system output and the expected value. Closed loop control has the advantages of high control accuracy and strong anti-interference ability, but it also has the disadvantages of high system complexity and high cost.
Position closed-loop control: Position closed-loop control measures the real-time position of the mechanical system, compares it with the expected position, and adjusts the control quantity based on the deviation. Position closed-loop control has the characteristics of high control accuracy and fast response speed, and is widely used in high-precision machine tools, robots, and other fields.
Speed closed-loop control: Speed closed-loop control measures the real-time speed of the mechanical system, compares it with the expected speed, and adjusts the control quantity based on the deviation. Speed closed-loop control has the advantages of high control accuracy and strong anti-interference ability, but it also has the problem of large control delay.
Acceleration closed-loop control: Acceleration closed-loop control measures the real-time acceleration of a mechanical system, compares it with the expected acceleration, and adjusts the control variable based on the deviation. Acceleration closed-loop control has the characteristics of high control accuracy and fast response speed, but at the same time, it also has the problem of high system complexity.
3、 Adaptive control
Adaptive control is an intelligent form of control, whose core idea is to automatically adjust control strategies and parameters based on the real-time performance of the system and changes in the external environment. Adaptive control has the advantages of high control accuracy, strong anti-interference ability, and strong adaptability, but at the same time, it also has the problems of high algorithm complexity and difficult implementation.
Adaptive PID control: Adaptive PID control adjusts the proportional, integral, and derivative parameters of the PID controller online to adapt to the dynamic characteristics of the system and changes in the external environment. Adaptive PID control has the characteristics of high control accuracy and strong anti-interference ability, and is widely used in industrial automation, robotics and other fields.
Adaptive fuzzy control: Adaptive fuzzy control fuzzifies the input and output of the system through fuzzy logic, and then automatically adjusts the control strategy and parameters according to fuzzy rules. Adaptive fuzzy control has the characteristics of high control accuracy, strong anti-interference ability, and strong adaptability, but at the same time, it also has the problems of high algorithm complexity and difficult implementation.
4、 Predictive control
Predictive control is a model-based control form, whose core idea is to establish a mathematical model of the system, predict the dynamic behavior of the system in the future, and adjust the control quantity based on the prediction results. Predictive control has the advantages of high control accuracy, strong anti-interference ability, and strong adaptability, but at the same time, it also has the problems of difficult model establishment and high computational complexity.
Model Predictive Control (MPC): Model predictive control establishes a mathematical model of the system to predict its dynamic behavior over a period of time in the future, and adjusts the control variables based on the predicted results. MPC has the characteristics of high control accuracy, strong anti-interference ability, and strong adaptability, and is widely used in fields such as chemical engineering, power, and transportation.
Neural network predictive control: Neural network predictive control models and predicts the dynamic behavior of the system by training the neural network, and then adjusts the control variable based on the prediction results. Neural network predictive control has the characteristics of high control accuracy, strong anti-interference ability, and strong adaptability, but at the same time, it also has the problems of difficult training and high computational complexity.
5、 Intelligent control
Intelligent control is a form of control based on artificial intelligence technology, whose core idea is to achieve intelligent control of complex systems by imitating human thinking and behavior. Intelligent control has the advantages of high control accuracy, strong anti-interference ability, and strong adaptability, but at the same time, it also has the problems of high algorithm complexity and difficult implementation.
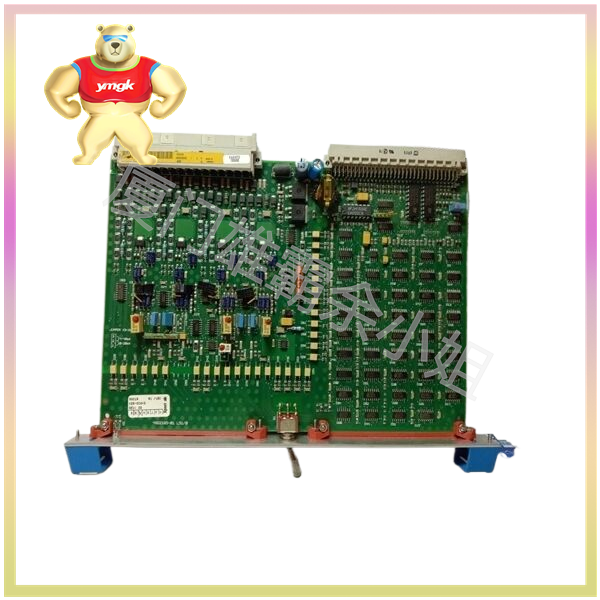
Genetic Algorithm Control: Genetic algorithm control optimizes control strategies and parameters by simulating natural selection and genetic mechanisms. Genetic algorithm control has the characteristics of high control accuracy, strong anti-interference ability, and strong adaptability, and is widely used in industrial automation, robotics, and other fields.
Deep learning control: Deep learning control models and predicts the dynamic behavior of a system by training deep neural networks, and then adjusts the control variables based on the predicted results. Deep learning control has the characteristics of high control accuracy, strong anti-interference ability, and strong adaptability, but at the same time, it also has the problems of high training difficulty and high computational complexity.
Summary:
There are various forms of control for motion controllers, each with its specific application scenarios and advantages. In practical applications, it is necessary to choose a suitable controller based on factors such as system performance requirements, cost budget, and implementation difficulty.