DC motor controller is a special type of electrical equipment that converts electrical energy into mechanical energy. DC motors receive electrical energy by using DC power and then convert this energy into automatic rotation of the motor. DC motors are almost ubiquitous, utilizing the magnetic field generated by the generated current to drive the rotor fixed on the output shaft. The speed and output torque depend on the motor design and electrical input.
How does the DC motor controller work?
The power and size of DC motors vary, and according to different mechanisms, they can be used for electric hoists and elevators, electric vehicles, and toys. A DC motor consists of two basic parts: the armature and the stator. The stator is the fixed part of the motor, while the armature is the rotating part. In addition to using coils, DC motors also use fixed magnet groups in the stator, and current flows through the circuit of the wires, thereby generating aligned electromagnetic fields. One or more coil windings of insulated wire are wrapped around the iron core of the motor to concentrate the magnetic field. The winding of the insulated wire is connected to a rotary electrical switch (commutator), which continues to apply current to the coil winding. The rotating electrical switch allows each armature coil to be energized, thereby generating torque or stable rotational force. After sequentially opening and closing the coils, a magnetic field will be generated that interacts with different areas of the fixed magnet, thereby generating torque. These basic working principles allow DC motors to convert electrical energy from DC to mechanical energy that can be used to propel equipment, all through rotational motion.
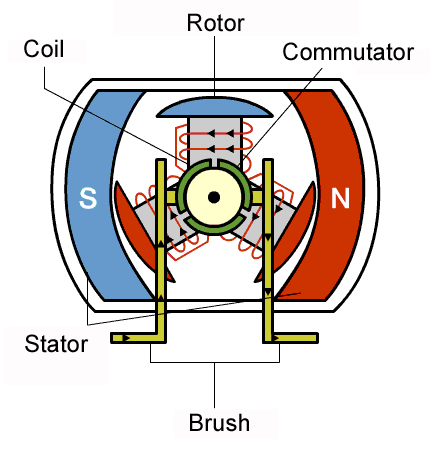
Who invented the DC motor controller?
DC motor is an outstanding electrical device that has completely changed people’s lives in many different ways, but who is the inventor of DC motor? Like all other innovations, many people have made a difference by developing other devices. In the United States, Thomas Davenport was the inventor of the first electric motor. In 1837, Davenport was the first person to apply for a patent for a usable motor. However, Davenport was not the first person to manufacture motors in this way, as other European inventors had already developed more powerful motors earlier. The reason why Davenport is praised as the original inventor is because he applied for a patent earlier. In 1834, Jacobi Moritz had already proposed a motor with higher power than Davenport (three times the power). One year later, Sibrandus Stratich and Christopher Becker demonstrated the practical application of motors.
Types of DC motor controllers and DC motor controls
Brushless DC motor
Also known as synchronous DC motor or electronic commutation motor, the main difference between these types of motors is that they lack a commutator, which is replaced by a servo mechanism that can detect and subsequently adjust the rotor angle. Brushless DC motors are durable and safe.
Brushed DC motor
These are the earliest DC motors, dating back to their original design. Although they are still popular in paper machines, cranes, and rolling mills, they have gradually disappeared recently.
Parallel DC motor
This is a brushed motor whose excitation winding is connected in parallel with the armature. Due to the parallel winding, they have lower current, and parallel motors have found many uses in various applications that require constant torque, such as mixers, conveyors, and cranes.
Series connected DC motor
These are the final varieties, and the excitation winding connected in series distinguishes them from parallel motors, which means that the armature current will indeed pass through the excitation winding, resulting in faster speed. Series DC motors are the ideal choice for tasks that require high starting torque.
When it comes to DC motor control, the following are the most commonly used methods:
Direction controller: H-bridge
The H-bridge circuit is one of the simplest methods for controlling a DC motor. In such a motor, four paired control switches can be found, and when either pair is closed, they immediately complete the circuit and then supply power to the motor. The H-bridge can also control the speed.
Speed controller: Pulse Width Modulation (PWM)
The PWM circuit changes the speed of the motor by simulating the increase or decrease of the power supply. PWM is easy to apply and cost-effective, which is one aspect of continuously controlling the motor speed. These controllers work by sending periodic pulses to the motor, and when using conventional pulse coil inductance to bring a certain constrained smoothing effect, the motor is like being powered by high or low voltage.
Armature controller: Variable resistor
This is another way to affect the speed of a DC motor, where the current fed through the armature or excitation coil changes. When the coil current changes, the speed of the output shaft also changes, and a variable resistor can change the current, thereby increasing the speed.
What to know when purchasing a DC motor
Before purchasing a DC motor, some basic considerations need to be taken into account. The following are some key factors to consider: the higher the energy, the greater the torque, and the energy keeps the net current flowing in a single direction. Check the recommended DC motor tension in the user manual. Current provides power to the motor, and excessive current can be dangerous as it can damage the motor. Before using a DC motor controller, make sure to understand its operating current and stalling current. The speed of the motor is somewhat complex. The motor operates effectively at high speeds, but if gear transmission is required, this cannot be achieved. Increasing gears will not limit the efficiency of the motor. Therefore, torque and speed reduction also need to be considered.
Why choose a DC motor?
When choosing to use AC motors, it is strongly recommended to choose DC motors as the first choice, as they have some advantages over AC motors. For example, when high starting torque is required to drive high inertia loads, they are excellent and different from AC motors, they are easy to control the speed of DC motors.
When DC motors require power from low-voltage DC sources such as solar panels or batteries, they are also an ideal choice. If you quickly reverse the direction, you will find that a DC motor is very suitable for use. Unlike AC motors, DC motors can be easily and quickly started and stopped.
Application Fields of DC Motor Controllers
There are various DC motors on the market now, and we widely use them. At home, DC motors can be used in toys, tools, and other household appliances. In the industrial field, their needs include running across turntables to conveyor belts, as well as reversing. DC motors are used to provide power to pumps based on their excellent motion responsiveness and easy variable speed characteristics. Due to their energy-saving mechanism, they are the preferred choice for fans. DC motor toys have multiple voltages, therefore requiring different types of movements and speeds. DC motors are preferred for electric vehicles due to their durability and energy efficiency. Electric bicycles are equipped with DC motors in both the rear and front wheel hubs to achieve the required power level and torque.