1、 Composition of Electrical Control System for Industrial Robots
Controller: The controller is the core component of the electrical control system for industrial robots, responsible for receiving input signals, processing data, and outputting control signals. Controllers typically use high-performance microprocessors or computer systems with powerful computing power and stability.
Sensor: A sensor is a sensing element in the electrical control system of industrial robots, used to detect the robot’s motion status, environmental information, etc. Common sensors include position sensors, speed sensors, force sensors, visual sensors, etc.
Driver: The driver is the executing component of the electrical control system of industrial robots, responsible for converting the control signals output by the controller into the motion of the robot. Common drivers include servo motor drivers, stepper motor drivers, hydraulic drivers, etc.
Communication interface: A communication interface is a channel for data exchange between the electrical control system of industrial robots and other devices or systems. Common communication interfaces include Ethernet, serial communication, fieldbus, etc.
Human machine interface: The human machine interface is the interface for the electrical control system of industrial robots to interact with operators, usually including touch screens, keyboards, displays, etc.
2、 Functions of Electrical Control System for Industrial Robots
Motion control: The electrical control system of industrial robots can achieve precise control of the robot’s motion trajectory, speed, acceleration and other parameters to meet the needs of different production tasks.
Task planning: The electrical control system of industrial robots can automatically plan the robot’s motion trajectory and operation sequence according to the requirements of production tasks, improving production efficiency.
Fault diagnosis: The electrical control system of industrial robots can monitor the operating status of the robots in real time, and promptly alarm and diagnose faults when abnormal situations are detected, ensuring the continuity and stability of production.
Safety protection: The electrical control system of industrial robots has safety protection functions, which can prevent accidents during the operation of robots and protect the safety of operators and equipment.
Data management: The electrical control system of industrial robots can collect, store, analyze, and process data during the production process, providing data support for production management.
3、 Characteristics of Electrical Control System for Industrial Robots
Highly integrated: The electrical control system of industrial robots integrates various components such as controllers, sensors, drivers, etc. together to form a complete control system, improving the stability and reliability of the system.
Real time performance: The electrical control system of industrial robots has real-time performance, can quickly respond to input signals, and achieve precise control of robot motion.
Flexibility: The electrical control system of industrial robots can flexibly adjust control strategies and parameters according to different production tasks and environmental requirements, meeting diverse production needs.
Intelligence: With the development of artificial intelligence technology, industrial robot electrical control systems have gradually acquired certain intelligent functions, such as self-learning, adaptive control, etc.
Networking: The electrical control system of industrial robots can achieve network connection with other devices or systems, realize data sharing and collaborative control, and improve production efficiency and quality.
4、 The Development Trend of Electrical Control Systems for Industrial Robots
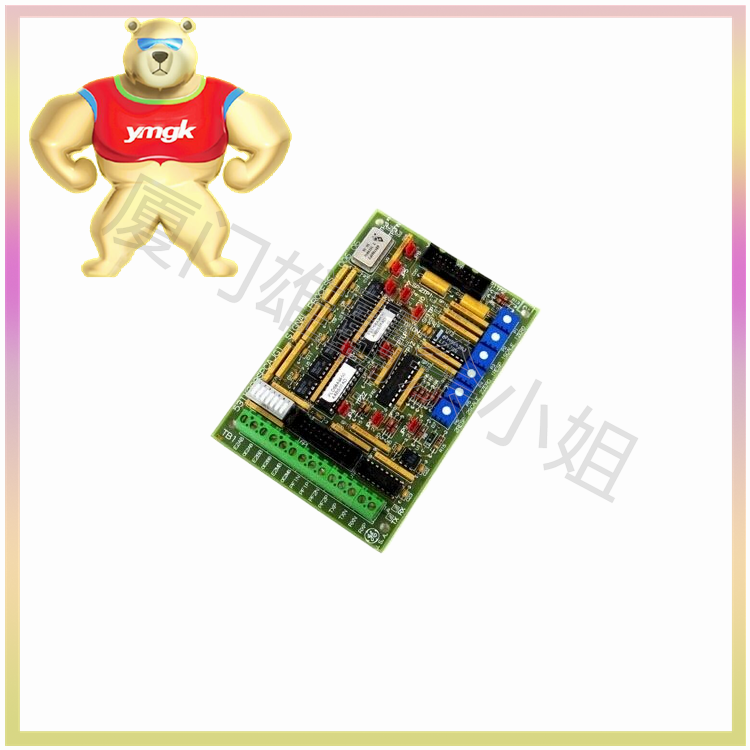
High performance: With the continuous expansion of industrial robot applications, the performance requirements for electrical control systems are also increasing. The future industrial robot electrical control system will have higher computing power, more precise control accuracy, and stronger stability.
Modular design: In order to improve the flexibility and scalability of industrial robot electrical control systems, modular design will become a development trend. Through modular design, various components of the control system can be quickly combined and adjusted according to different application requirements.
Intelligent upgrade: With the continuous development of artificial intelligence technology, the electrical control system of industrial robots will become more intelligent, with functions such as self-learning and adaptive control, improving production efficiency and quality.
Networked collaboration: Industrial robot electrical control systems will pay more attention to network connections and collaborative control with other devices or systems, achieving data sharing and optimizing production processes.
Safety improvement: With the increasing application of industrial robots in various fields, safety issues are also receiving increasing attention. The future industrial robot electrical control system will pay more attention to safety protection functions to ensure the safety and stability of production.
In short, the electrical control system of industrial robots is an important component of industrial robots, and the optimization and upgrading of its architecture is of great significance for improving production efficiency and quality. With the continuous development of technology, the electrical control system of industrial robots will move towards high-performance, modular design, intelligent upgrading, networked collaboration, and improved safety, providing stronger support for industrial automation and intelligent manufacturing.