Programmable Logic Controller (PLC) is an electronic device widely used in the field of industrial automation. It controls mechanical equipment by receiving input signals, processing logic operations, and outputting control signals. This article will provide a detailed introduction to the working principle, composition, programming methods, and practical applications of PLC.
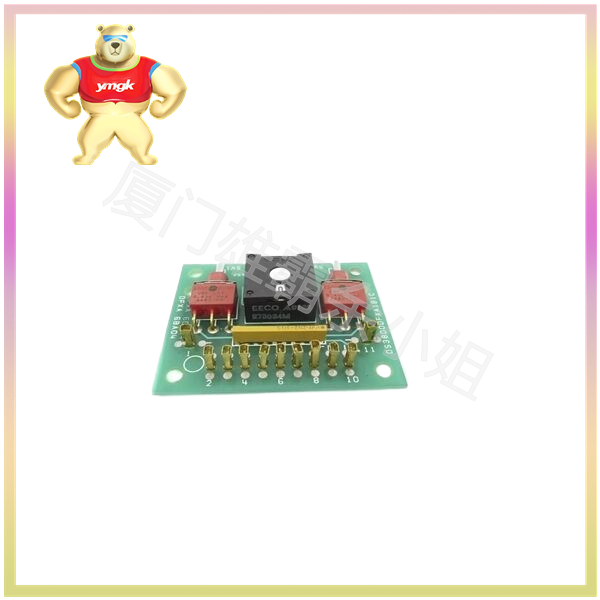
1、 The working principle of PLC
Input processing: PLC receives signals from external devices such as sensors and switches through input interfaces. These signals can be digital signals, such as switch status, or analog signals, such as temperature, pressure, etc.
Logical operation: The central processing unit (CPU) inside the PLC performs logical operations on input signals according to preset programs. These programs are usually written by users through programming software, including conditional judgment, loop control, data calculation, etc.
Output control: Based on the results of logical operations, PLC sends control signals to actuators, drivers, and other devices through output interfaces to achieve control of mechanical equipment. These signals can be switch signals used to control the start and stop of equipment, or analog signals used to adjust the operating parameters of the equipment.
Cyclic scanning: The working process of PLC is cyclic scanning, which continuously repeats the process of input processing, logical operations, and output control. This cyclic scanning method can ensure real-time control of the equipment by the PLC.
2、 Composition of PLC
Central Processing Unit (CPU): The CPU is the core component of a PLC, responsible for executing programs, processing data, and controlling the work of other components.
Input/output module: The input module is used to receive external signals, and the output module is used to send control signals to external devices. According to the signal type, input/output modules can be divided into digital modules and analog modules.
Power module: Provides stable power to the PLC to ensure its normal operation.
Memory: Used for storing programs and data. The memory of PLC usually includes system memory and user memory. System memory is used to store system programs, while user memory is used to store programs and data written by users.
Communication interface: used to achieve communication between PLC and other devices or upper computer. Common communication interfaces include Ethernet, serial port, fieldbus, etc.
3、 Programming methods for PLC
Ladder Diagram (LD): A ladder diagram is a graphical programming language that represents logical relationships in a way similar to electrical control circuits, making it easy to understand and program.
Instruction List (IL): Instruction List is a text-based programming language that uses mnemonics to represent various operational instructions, suitable for complex logical operations and data processing.
Function Block Diagram (FBD): FBD is a graphical programming language based on functional blocks, which decomposes a program into multiple functional blocks for modular design and reuse.
Structured Text (ST): Structured text is a text-based programming language similar to high-level programming languages, which supports programming structures such as variables, data types, conditional judgments, and loop control, and is suitable for complex algorithm implementation.
4、 The practical application of PLC
Mechanical equipment control: PLC is widely used for controlling various mechanical equipment, such as conveyor belts, robots, CNC machine tools, etc. Through the control of PLC, automatic operation, parameter adjustment, fault diagnosis and other functions of the equipment can be achieved.
Process control: PLC is also widely used in process control fields such as chemical, petroleum, and power. It can monitor and control various parameters in the production process in real time, such as temperature, pressure, flow rate, etc., to ensure the stability and safety of the production process.
Building automation: PLC is used in building automation systems to control lighting, air conditioning, elevators, and other equipment, improving energy efficiency and comfort.
Transportation: In the field of transportation, PLC can be used to control traffic signals, switches, station equipment, etc., improving transportation efficiency and safety.
5、 Advantages of PLC
High reliability: PLC adopts industrial grade components and strict design standards, with high reliability and stability.
Real time performance: PLC adopts a cyclic scanning working mode, which can respond to changes in external signals in real time and achieve precise control of equipment.
Flexibility: PLC has rich input/output modules and communication interfaces, which can adapt to the control needs of various devices.
Usability: The programming language of PLC is simple and easy to understand, and users can quickly implement control logic through graphical or textual programming.
Scalability: PLC systems can add more modules and devices as needed to achieve system expansion and upgrading.
6、 The Development Trend of PLC
Integration: With the development of technology, PLC systems are gradually integrating with other automation equipment and information systems to achieve more efficient production and management.
Intelligence: PLC systems are introducing technologies such as artificial intelligence and big data to achieve intelligent optimization and fault prediction of production processes.
Networking: PLC system is gradually connected to the Internet to realize remote monitoring, diagnosis and control.
Greening: In order to reduce energy consumption and environmental pollution, PLC systems are developing towards energy conservation and environmental protection.