Distributed Control System (DCS) and Programmable Logic Controller (PLC) are two important control technologies in the field of modern industrial automation. They share similarities in many aspects, but there are also significant differences in certain key aspects. This article will provide a detailed introduction to the differences and connections between DCS and PLC.
Definition of DCS and PLC
DCS (Distributed Control System) is a distributed control system composed of multiple control nodes, which are connected together through a network to achieve centralized control of the entire production process. DCS systems are typically used in large, complex industrial processes such as petroleum, chemical, and power industries.
PLC (Programmable Logic Controller) is a type of programmable logic controller, which is a computer specifically designed for industrial control. PLC controls the production process by receiving input signals, executing user written programs, and then outputting control signals. PLC is widely used in various industrial fields, such as manufacturing, construction, transportation, etc.
The difference between DCS and PLC
2.1 System Structure
The DCS system adopts a distributed structure, consisting of multiple control nodes that are connected together through a network. Each control node can independently complete a portion of the control tasks, achieving local control over the production process. PLC systems usually adopt a centralized structure, where all control tasks are completed on one or several PLCs.
2.2 Control ability
DCS systems have stronger control capabilities and can handle more complex control tasks. DCS system can achieve centralized control of the entire production process, including real-time data acquisition, data processing, control strategy execution and other functions. The PLC system is mainly used to implement simple control tasks, such as switch control, counting control, etc.
2.3 Communication Capability
DCS system has stronger communication capability and can achieve interconnection and intercommunication with various devices and systems. DCS systems typically use standard communication protocols such as Modbus, Profibus, etc., which can facilitate communication with other devices and systems. The communication capability of PLC systems is relatively weak, usually only able to communicate with devices of the same brand.
2.4 Scalability
DCS systems have better scalability and can flexibly increase or decrease control nodes according to the needs of the production process. However, the scalability of PLC systems is relatively poor, and the entire system usually needs to be replaced to meet the needs of the production process.
2.5 Application Fields
DCS systems are mainly used in large and complex industrial processes, such as petroleum, chemical, power and other industries. PLC systems are widely used in various industrial fields, such as manufacturing, construction, transportation, etc.
The connection between DCS and PLC
3.1 Control Function
Although DCS and PLC have differences in system structure, control capabilities, and other aspects, their basic control functions are similar. Both DCS and PLC need to receive input signals, execute control strategies, and then output control signals to achieve control over the production process.
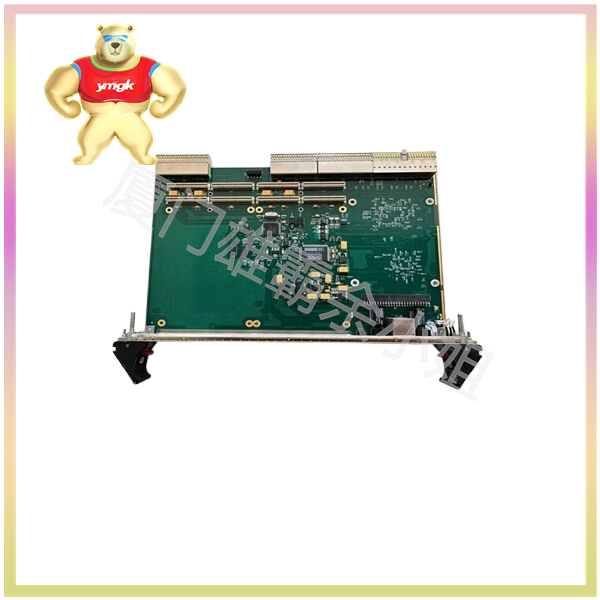
3.2 Control Strategy
Both DCS and PLC can implement various control strategies, such as PID control, fuzzy control, adaptive control, etc. Users can choose appropriate control strategies based on their own needs to achieve optimized control of the production process.
3.3 Programming Language
Both DCS and PLC support multiple programming languages, such as ladder diagrams, sequential function diagrams, instruction lists, etc. Users can choose the appropriate programming language for programming based on their habits and needs.
3.4 Human Computer Interface
Both DCS and PLC can be connected to various human-machine interfaces (HMI) to achieve real-time monitoring and control of the production process. Users can conveniently view real-time data of the production process, adjust control parameters, and achieve optimized control of the production process through the human-machine interface.
conclusion
DCS and PLC are two important control technologies in the field of modern industrial automation. They have significant differences in system structure, control capabilities, communication capabilities, etc., but they share similarities in basic control functions, control strategies, programming languages, human-machine interfaces, and other aspects. In practical applications, users need to choose appropriate control technologies based on their own needs and the characteristics of the production process to achieve optimized control of the production process.
In short, DCS and PLC each have their own advantages and disadvantages, and they have their own strengths in different application scenarios. By deeply understanding the differences and connections between DCS and PLC, users can better utilize these two technologies, improve production efficiency, reduce production costs, and achieve optimization and upgrading of industrial automation.