Servo drives all use digital signal processors (DSPs) as the control core, which can implement complex control algorithms, achieve digitization, networking, and intelligence. Power devices commonly use drive circuits designed with intelligent power modules (IPMs) as the core. IPMs integrate drive circuits internally and have fault detection and protection circuits for overvoltage, overcurrent, overheating, undervoltage, etc. Soft start circuits are also added to the main circuit to reduce the impact of the start-up process on the driver.
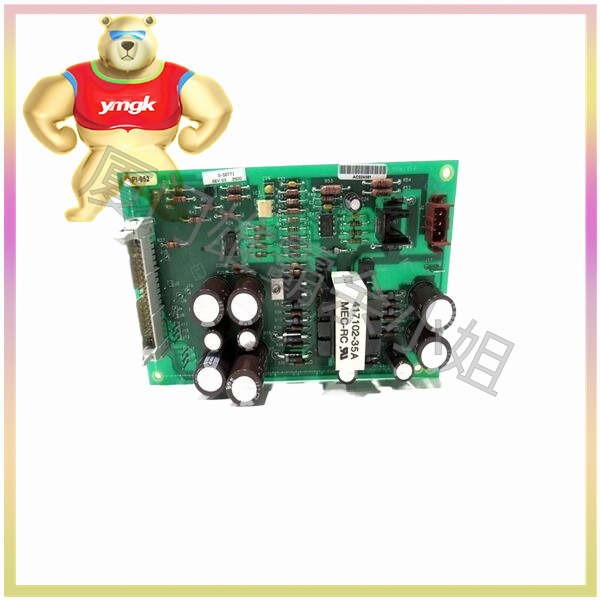
Firstly, the power driving unit rectifies the input three-phase power or mains power through a three-phase full bridge rectifier circuit to obtain the corresponding DC power. After rectification, the three-phase power or mains power is used to drive the AC servo motor through a three-phase sine PWM voltage type inverter frequency conversion. The entire process of the power drive unit can be simply described as the AC-DC-AC process, and the main topology circuit of the rectifier unit (AC-DC) is a three-phase full bridge uncontrolled rectifier circuit.
Generally, servos have three control modes: position control mode, torque control mode, and speed control mode.
- Position control: The position control mode generally determines the speed of rotation by the frequency of external input pulses, and determines the angle of rotation by the number of pulses. Some servos can also directly assign values to speed and displacement through communication. As the position mode can have strict control over both speed and position, it is generally applied to positioning devices.
- Torque control: The torque control method is to set the output torque of the motor shaft to the outside through external analog input or direct address assignment. The set torque can be changed by instantly changing the analog setting, or by changing the corresponding address value through communication.
The application is mainly in winding and unwinding devices that have strict requirements for the material, such as winding devices or fiber optic equipment. The torque setting should be changed at any time according to the change of the winding radius to ensure that the material’s stress does not change with the change of the winding radius.
- Speed mode: The rotational speed can be controlled through analog input or pulse frequency. In the outer loop PID control with upper control device, the speed mode can also be used for positioning, but the position signal of the motor or the position signal of the direct load must be fed back to the upper control for calculation. The position mode also supports direct load outer ring detection of position signals. At this time, the encoder at the motor shaft end only detects the motor speed, and the position signal is provided by the direct detection device at the final load end. The advantage of this is that it can reduce errors in the intermediate transmission process and increase the positioning accuracy of the entire system.
If there are no requirements for the speed and position of the motor, as long as a constant torque is output, of course, torque mode is used.
If there are certain precision requirements for position and speed, but real-time torque is not very concerned, it is not convenient to use torque mode. It is better to use speed or position mode.
If the upper controller has good closed-loop control function, the speed control effect will be better. If the requirements are not very high or there is basically no real-time requirement, the position control method should be adopted.