Servo drive
(1) Definition and Function
A servo driver, also known as a “servo controller” or “servo amplifier”, is a type of controller specifically designed to control servo motors. Its function is similar to that of a frequency converter acting on a regular AC motor, and it is part of a servo system mainly used in high-precision positioning systems. The servo driver receives control signals (such as pulse signals or analog signals) and converts them into electrical signals to drive the servo motor, thereby achieving precise control of the servo motor.
(2) Composition and Working Principle
Servo drives typically consist of three parts: power supply, arithmetic unit, and power output. Among them, the power supply is responsible for providing stable electrical energy; The arithmetic unit is responsible for receiving control signals and processing them to generate electrical signals that drive servo motors; The power output part is responsible for converting electrical signals into the current or voltage required by the servo motor.
The mainstream servo drives use digital signal processors (DSPs) as the control core, which can implement complex control algorithms, achieve digitization, networking, and intelligence. Power devices commonly use driver circuits designed with intelligent power modules (IPMs) as the core, which have fault detection and protection circuits for overvoltage, overcurrent, overheating, undervoltage, etc., to ensure the stable operation of the driver.
(3) Application and technical characteristics
Servo drives are widely used in industrial robots, CNC machine tools, automation equipment, and other fields. Its main technical features include high-precision control, high dynamic response, safety and stability, and flexibility and adjustability. For example, by controlling the servo motor through position, speed, and torque, high-precision positioning of the transmission system can be achieved.
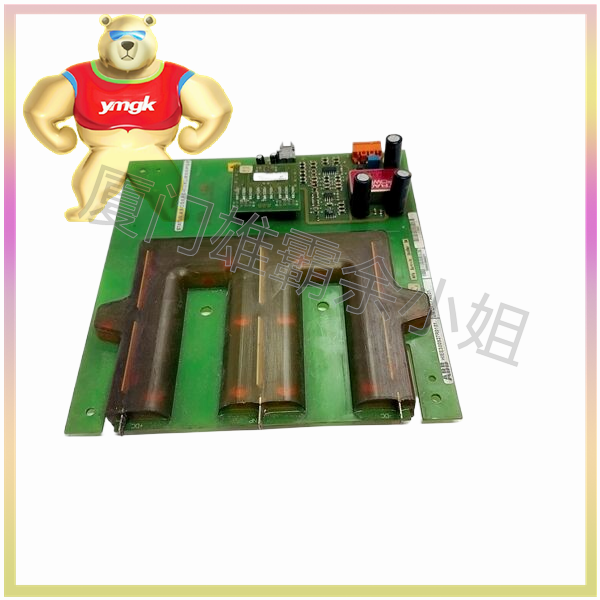
Servo control system
(1) Definition and Function
A servo control system is a complex system composed of multiple parts, including motion controllers, servo motors, drivers, sensors, etc. Its main function is to measure and provide real-time feedback on the motion status of the controlled object through sensors based on input command signals. After processing by the controller, it outputs control signals to drive the servo motor to move according to predetermined trajectories, speeds, and accelerations, achieving precise control.
(2) Composition and Working Principle
Servo control systems generally consist of controllers, encoders, sensors, actuators, and other components. Among them, the controller is responsible for receiving instruction signals and processing them to generate control signals; The encoder is responsible for measuring the position and speed of the servo motor and feeding back the measured values to the controller; Sensors are responsible for real-time measurement of the motion status of the controlled object; The executing agency is responsible for converting the control signal into the motion of the servo motor.
The working principle of servo control system is based on feedback control principle. By continuously comparing the command signal and feedback signal, the deviation signal is calculated, and the control signal is adjusted accordingly, so that the motion state of the controlled object gradually approaches the state required by the command signal.
(3) Application and technical characteristics
Servo control systems are widely used in fields such as aerospace, precision manufacturing, and robotics technology. Its main technical features include high-precision control, high dynamic response, high stability, and easy control integration. For example, in the aerospace field, servo control systems can achieve high-precision control of aircraft attitude; In the field of precision manufacturing, servo control systems can achieve precise control over the machining process; In the field of robotics, servo control systems can achieve precise control of robot motion.
The difference between servo drive and servo control system
(1) Different functional positioning
Servo driver is an important component of servo control system, mainly responsible for converting control signals into electrical signals to drive servo motors; The servo control system is a complete system, including multiple parts, responsible for achieving precise control functions.
(2) Different technical characteristics
Servo drivers focus on precise driving and control of servo motors; The servo control system, on the other hand, places more emphasis on the stability and control accuracy of the entire system.
(3) Different application scope
Servo drives are mainly used in situations where precise control of servo motors is required; And servo control systems are more widely used in various fields that require precise control.
5、 Conclusion
In summary, servo drives and servo control systems play important roles in the fields of industrial automation and precision control. They each have different functions and technical characteristics, and work together to achieve high-precision control effects. In practical applications, it is necessary to select appropriate devices and systems based on specific needs and scenarios.