(1) Definition and Function
An industrial controller is an electronic device used in industrial automation systems, responsible for receiving, processing, and sending control signals to achieve precise control of industrial equipment. The main functions of industrial controllers include task allocation, resource scheduling, data processing, monitoring, and management.
Task allocation: Industrial controllers can assign tasks to other devices, such as motors, sensors, etc., and ensure that they are executed correctly.
Resource scheduling: The controller allocates resources such as electricity, bandwidth, etc. to other devices to ensure their efficient and stable operation.
Data processing: The controller can collect and process data from other devices, such as temperature, pressure, speed, etc., and make corresponding responses based on it.
Monitoring and Management: The controller can monitor the status and behavior of other devices and take necessary measures to ensure their normal operation.
(2) Structure and Composition
Industrial controllers typically consist of microprocessors, memory, input/output interfaces, communication interfaces, and other components. The microprocessor is the core of the controller, responsible for executing control algorithms and logical operations; Memory is used to store programs and data; Input/output interfaces are used to connect other devices such as motors, sensors, etc; The communication interface is used to communicate with other controllers or upper computers.
(3) Application scenarios
Industrial controllers are widely used in various industrial automation systems, such as production line control, robot control, process control, etc. In these applications, industrial controllers monitor and control the production process in real-time by receiving signals from sensors, actuators, and other devices to ensure the stability of the production process and product quality.
3、 Motor Overview
(1) Definition and Function
An electric motor is a device that converts electrical energy into mechanical energy and is an important executing component in industrial automation systems. The main function of a motor is to convert the control signals emitted by the controller into mechanical motion, thereby driving various industrial equipment or mechanical devices.
(2) Structure and Composition
The motor is mainly composed of stator, rotor, bearings, end caps, and other parts. The stator is a fixed part of the motor, usually composed of an iron core and windings; The rotor is the rotating part of a motor, usually made of conductive material; Bearings are used to support the rotor and allow it to rotate; The end cap is used to secure the internal components of the motor and protect it from external influences.
(3) Types and Applications
Electric motors can be classified into DC motors, AC motors, servo motors, etc. Among them, AC motors are widely used in various industrial applications due to their advantages of simple structure, high reliability, and low cost. Servo motors are widely used in applications that require high-precision positioning and control, such as CNC machine tools, robots, etc., due to their characteristics of high precision, high speed, and high reliability.
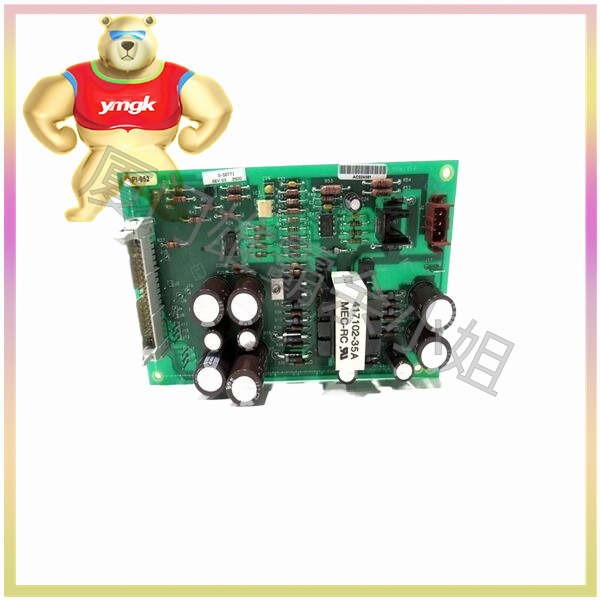
4、 The difference between industrial controllers and motors
(1) Functional differences
Industrial controllers are mainly responsible for receiving, processing, and sending control signals to achieve precise control of industrial equipment; And the motor is a device that converts electrical energy into mechanical energy, responsible for executing the instructions of the controller and driving various industrial equipment or mechanical devices. Simply put, industrial controllers are the “brain” responsible for decision-making and command; And the motor is the “limbs” responsible for execution and movement.
(2) Structural differences
Industrial controllers typically consist of microprocessors, memory, input/output interfaces, communication interfaces, and other components; The motor is mainly composed of stator, rotor, bearings, end caps, and other parts. The structural differences between the two reflect their different roles and functions in industrial automation systems.
(3) Differences in application scenarios
Industrial controllers are widely used in various industrial automation systems, such as production line control, robot control, process control, etc; Electric motors are widely used in various situations that require mechanical motion, such as CNC machine tools, robots, conveyor belts, etc. Although both play important roles in industrial automation systems, their application scenarios and focus are different.
5、 Summary
Industrial controllers and motors are two indispensable components in industrial automation systems. They have essential differences in terms of functionality, structure, and application scenarios. By delving into the differences between industrial controllers and motors, we can better understand their roles and functions in industrial automation systems, providing strong support for the design and application of industrial automation systems.