The main factors affecting the reliability of PLC control systems
The reliability of PLC control systems is usually measured by Mean Time Between Failure (WIBF). It represents the average time interval between the repair of a system malfunction and the next occurrence of a malfunction. The PLC device itself is very reliable, and the interference of the PLC control system is mainly caused by external links and improper hardware configuration. One is the power frequency interference on the power supply side, which enters the PLC device from the power supply and causes abnormal system operation; The second is the interference of electrostatic or magnetic field coupling in line transmission, as well as the radiation interference of surrounding high-frequency power sources. Electrostatic coupling occurs through parasitic capacitance between signal lines and power lines, magnetic field coupling occurs on parasitic mutual inductance between long wiring lines, and high-frequency radiation occurs through parasitic capacitance between high-frequency alternating magnetic fields and signals; The third is interference caused by improper grounding system of PLC control system. Therefore, in practical design, the following aspects are often considered: 1) protection of programs and data; 2) Adaptability to industrial production environment; 3) Fault safety principle, system independence principle, redundancy and fault-tolerant structure; 4) Real time and continuity during runtime.
Anti interference design of PLC control system
According to the main factors affecting the reliability of PLC control systems, in the development and design of PLC control systems, both system software and hardware should be considered to improve the reliability and anti-interference ability of the PLC control system. In practical production applications, the main consideration is the hardware anti-interference design of the control system.
The 3MZ203D machine tool is a bearing ring internal grinder. Based on actual production requirements and years of practical experience, relevant measures have been taken for the hardware anti-interference design and application of the PLC control system of the 3MZ203D internal grinder. The following is an introduction to this.
3.1 Suppressing interference introduced by the power system
In order to suppress the voltage fluctuations and power frequency interference caused by the start stop of large capacity equipment in the power grid, isolation transformers can be used and filtered, and all shielding layers should be well grounded. As shown in Figure 1.
3.2 Application of anti-interference design for installation and wiring
In places with significant changes in ground potential, PLC systems are subject to common mode interference, which can easily transform into series mode interference. Therefore, the design of the grounding system for the control system is particularly important. The grounding method of the control system adopts an independent grounding point, as shown in Figure 2. Attention should be paid when grounding: the grounding wire should be as short as possible and the cross-sectional area should be greater than 2mm; The grounding point should be as close as possible to the controller; The grounding wire should avoid the wires of the strong current circuit and the main circuit, and if it cannot be avoided, it should be crossed vertically; The grounding resistance should be less than 2 Ω.
PLC power lines, I/O power lines, input signal lines, output signal lines, AC lines, and DC lines should use their own cables and be wired separately as much as possible. Switch signal lines and analog signal lines should also be wired separately as much as possible. Moreover, the analog signal line should be shielded and the shielding layer of the cable should be grounded; Shielded cables should also be used for digital transmission lines, and the shielding layer of the cable should be grounded; When the input and output signal lines of AC and DC have to use the same wiring conduit, shielded cables should be used for the DC input and output signal lines, and the shielding layer should be grounded.
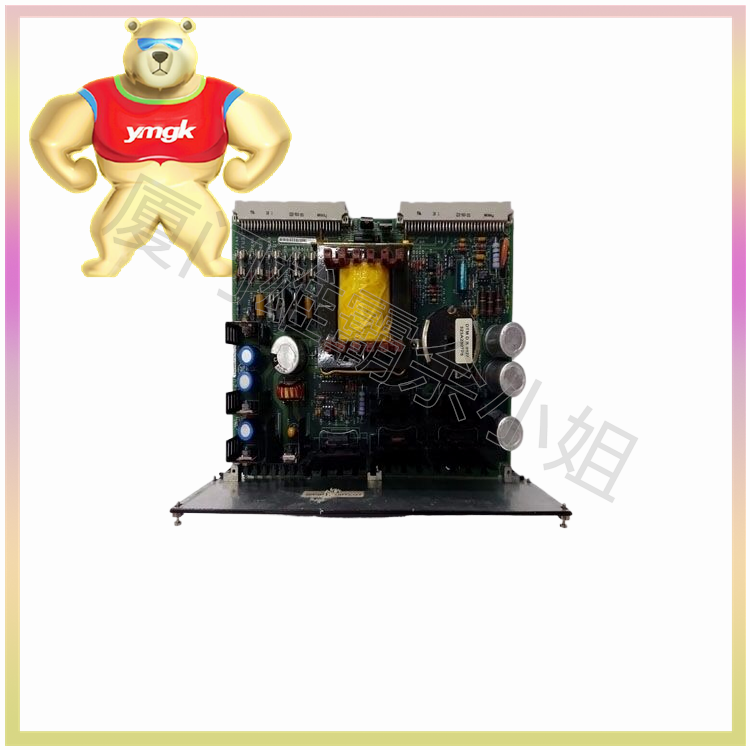
3.3 Anti interference design and application of input signals
The line to line interference (differential mode interference) of the input signal of the input device can be attenuated by the filter of the input module. However, the common mode interference between the input signal line and the ground can still cause the controller to malfunction due to the potential difference generated in the internal circuit of the controller. Therefore, in order to resist common mode F interference, the controller needs to be well grounded.
When the input signal source is an inductive component and the load characteristics of the output load are inductive components, in order to prevent the module from being damaged by recoil induced potential or surge current, capacitors C and resistors R are connected in parallel at both ends of the load for AC input signals, and freewheeling diodes VD are connected in parallel for DC input signals, as shown in Figure 3. In Figure 3 (a), the R and C parameters are generally selected as 120 Ω+0.1 μ F (when the load capacity is<10V · A) or 47 Ω+0.471 μ F (when the load capacity is>10V · A). In Figure 3 (b), the rated current of the diode is selected as 1A, and the rated voltage should be greater than three times the power supply voltage. For the interference of induced voltage, the methods of input voltage DC conversion or parallel connection of surge absorbers are used to suppress it [1].
3.4 Anti interference design of output signal
Connect surge absorbers in parallel at both ends of the load when dealing with inductive loads; In the case of a DC load, a current diode VD is connected in parallel at both ends of the load to suppress interference in the output signal, as shown in Figure 4. In Figure 4 (a), the closer the RC is to the load, the better the anti-interference effect. When the output of the PLC drives components such as solenoid valves, a solid-state relay (SSR) can be added between the output terminal and the solenoid valve for isolation. In addition, from the perspective of anti-interference, it is also important to choose the I/0 module appropriately. In situations with high interference, insulated I/O modules and modules equipped with surge absorbers can be used to effectively suppress ground interference in input and output signals.
3.5 Input/output signal leakage current ground handling
When the input signal source is a transistor or a photoelectric switch output type, if the output element is bidirectional or the transistor output and the external load is small, there will be a large ground leakage current when these output elements are turned off, which will prevent the input circuit and external load circuit from turning off, resulting in input and output signal grounding errors. For this purpose, parallel bypass resistors should be connected at the input and output terminals to reduce the input current of the PLC and the current on the external load, as shown in Figure 5.