Fieldbus Control System (FCS) is a new generation of control system developed in recent years, which adopts a fully distributed system architecture and completely delegates control functions to the field. In FCS, fieldbus instruments undertake the majority of control functions, while the control room is primarily responsible for advanced control functions. This structure makes FCS simpler in structure, reduces the use of I/O cards, and thus lowers the complexity and cost of the system.
In contrast, Distributed Control Systems (DCS) adopt a centralized and decentralized control system architecture. In DCS, key components such as operation stations, engineer stations, and on-site control stations are centralized in the control room, and on-site equipment is connected to the control room through a dedicated communication network. DCS achieves centralized management and decentralized control through a hierarchical control approach. Although DCS is relatively complex in structure, its stability and reliability have been widely recognized.
2、 Wiring method
There are significant differences in wiring methods between FCS and DCS. FCS adopts fieldbus technology, which connects multiple field instruments together through a pair of twisted pair cables to achieve digital signal transmission. This wiring method not only simplifies the wiring work of the system, reduces installation costs, but also improves the reliability and maintainability of the system. When it is necessary to add on-site control equipment, simply connect the new equipment to the existing twisted pair cable nearby, without the need for complex wiring work.
DCS, on the other hand, adopts the traditional analog signal transmission method, connecting field instruments with control room I/O cards through a two-wire system. This wiring method requires a large number of cables and junction boxes, which increases the complexity and cost of the system. Meanwhile, due to the susceptibility to interference and attenuation during analog signal transmission, DCS has certain limitations in terms of stability and reliability.
3、 Functional Features
In terms of functional characteristics, there are also significant differences between FCS and DCS. FCS disperses control functions to on-site devices, achieving integration of sensing measurement, compensation, computation, execution, and control functions. This design enables on-site equipment to have higher independence and autonomy, and can independently complete various control tasks. At the same time, FCS also adopts the open interconnection network technology, which enables equipment from different manufacturers or networks at the same level to connect and communicate with each other, and realizes information sharing and exchange.
DCS, on the other hand, adopts a centralized management and decentralized control approach, monitoring and managing on-site equipment through a control room. DCS has powerful data processing and computing capabilities, capable of real-time collection, processing, and storage of on-site data. At the same time, DCS also supports multiple communication protocols and network interfaces, which can connect and communicate with different types of devices. However, due to the fact that the control functions of DCS are mainly concentrated in the control room, the independence and autonomy of on-site equipment are relatively low.
4、 Safety and reliability
There are also certain differences between FCS and DCS in terms of safety and reliability. FCS adopts a fully distributed system architecture and fieldbus technology, which significantly improves the reliability and stability of the system. At the same time, FCS also supports functions such as hot backup and redundancy design, which can automatically switch to backup devices or backup systems to continue operating in the event of equipment failure. In addition, FCS also has powerful fault diagnosis and recovery capabilities, which can quickly locate and solve equipment failure problems.
DCS, on the other hand, adopts a centralized management and decentralized control approach. Although it has improved the reliability and stability of the system to a certain extent, there are still some potential safety hazards. For example, if key components in the control room fail or are attacked, it may lead to the paralysis or failure of the entire system. In addition, DCS also has certain limitations in fault diagnosis and recovery, which require the assistance of professional technical personnel for troubleshooting and resolution.
5、 Applicable scenarios and cost considerations
In terms of applicable scenarios, FCS and DCS each have their own applicable fields and scenarios. FCS is suitable for applications that require high independence of on-site equipment and require information sharing and exchange between devices, such as petrochemicals, power, metallurgy, and other fields. DCS is suitable for applications that require high requirements for centralized management and decentralized control in control rooms, such as chemical, pharmaceutical, water treatment, and other fields.
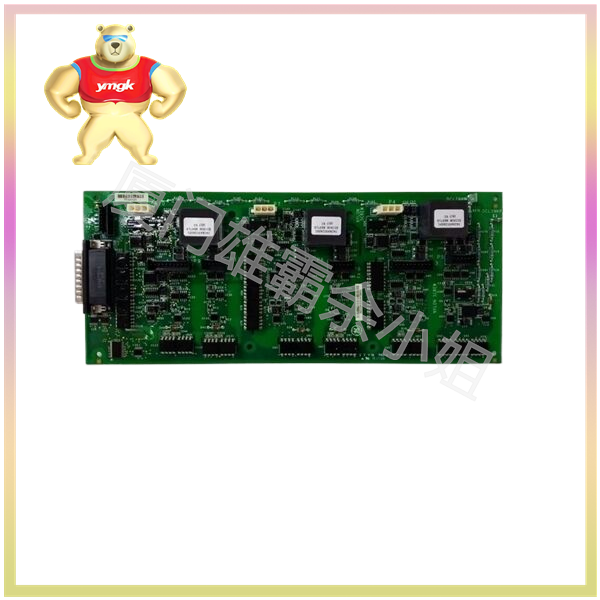
In terms of cost considerations, there are also certain differences between FCS and DCS. Due to the fully distributed system architecture and fieldbus technology adopted by FCS, its hardware cost is relatively low, but software cost may be higher. DCS, on the other hand, adopts a centralized management and decentralized control approach, with relatively high hardware costs but possibly lower software costs. In addition, due to the differences in functional characteristics, safety, and reliability between FCS and DCS, comprehensive consideration and selection are needed based on specific requirements in practical applications.
6、 Summary and Prospect
In summary, there are significant differences between fieldbus control systems (FCS) and distributed control systems (DCS) in terms of structure, wiring methods, functional characteristics, safety, and reliability. FCS has the advantages of simple structure, convenient wiring, integrated functionality, safety and reliability, and is suitable for situations where high independence of on-site equipment is required and information sharing and exchange between devices need to be achieved. DCS, on the other hand, has advantages such as centralized management, decentralized control, and strong data processing capabilities, making it suitable for situations where high requirements are placed on centralized and decentralized control in the control room.
In the future, with the continuous development of industrial automation technology and changing application requirements, FCS and DCS will also continue to evolve and improve. On the one hand, FCS will further improve its functionality and performance, enhance the reliability and stability of the system; On the other hand, DCS will continue to optimize its structure and functions, improving the integration and intelligence level of the system.