From the perspective of control methods, the control logic of the electrical control system adopts hardware wiring, which combines the series or parallel connection of relay mechanical contacts to form the control logic. The wiring is complex, bulky, and has high power consumption. After the system is constructed, it is difficult to change or add functions. In addition, the limited number of contacts in relays greatly limits the flexibility and scalability of electrical control systems. And PLC adopts computer technology, and its control logic is stored in memory in the form of programs. To change the control logic, only the program needs to be changed, so it is easy to change or add system functions. The system has few connections, small size, and low power consumption, and the so-called “soft relay” in PLC is essentially the state of the memory unit. Therefore, the number of contacts of the “soft relay” is infinite, and the flexibility and scalability of the PLC system are good.
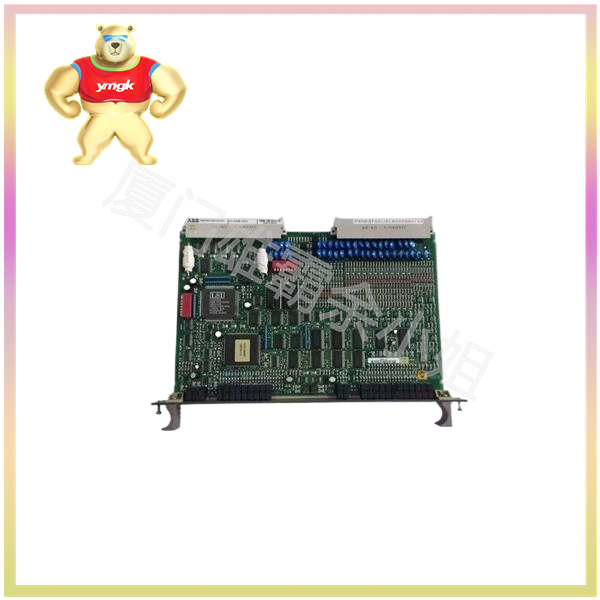
2) From the perspective of working mode, in the relay control circuit, when the power is turned on, all relays in the circuit are in a constrained state, that is, the relays that should be closed are closed at the same time, and the relays that should not be closed cannot be closed due to certain conditions. This working mode is called parallel working mode. The user program of PLC is executed in a certain order in a cyclic manner, so each soft relay is in a periodic cycle of scanning and connecting. The action sequence of each relay constrained by the same conditions is determined by the program scanning sequence. This working mode is called serial working mode.
3) From the perspective of control speed, relay control systems rely on the action of mechanical contacts to achieve control, with low operating frequencies and mechanical contact vibrations. And PLC controls semiconductor circuits through program instructions to achieve control, with fast speed, program instruction execution time in microseconds, and no contact jitter problems.
4) From the perspective of timing and counting control, the electrical control system uses the delay action of time relays for time control. The delay time of time relays is easily affected by environmental temperature and temperature changes, resulting in low timing accuracy. PLC uses semiconductor integrated circuits as timers, and clock pulses are generated by crystal oscillators with high accuracy and wide timing range. Users can set the timing value in the program according to their needs, which is easy to modify and not affected by the environment. PLC also has counting function, while electrical control systems generally do not have counting function.
5) From the perspective of reliability and maintainability, due to the use of a large number of mechanical contacts in electrical control systems, they suffer from mechanical wear, arc burns, etc., have a short lifespan, and have multiple system connections, resulting in poor reliability and maintainability. A large number of switch actions in PLC are completed by contactless semiconductor circuits, which have long lifespan and high reliability. PLC also has self diagnostic function, which can detect its own faults, display them to operators at any time, and dynamically monitor the execution of control programs, providing convenience for on-site debugging and maintenance.