1、 System performance requirements
Wide speed control range: Hydraulic servo systems need to have a wide speed control range to meet the speed control requirements under different working conditions. Generally speaking, the speed range of the system should be able to cover a wide range from extremely low speed to high speed to meet the requirements of various complex motion controls.
High positioning accuracy: The system should have high-precision positioning capability and be able to accurately locate the actuator to the predetermined position. This requires the system to have small position errors and repeated positioning errors to ensure the accuracy of processing or operation.
Sufficient transmission rigidity and high speed stability: Hydraulic servo systems should have high transmission rigidity and speed stability to ensure that the system can maintain a stable motion state under load changes or external disturbances. This helps to reduce the vibration and noise of the system and improve its dynamic performance.
Quick response, no overshoot: The system should be able to quickly respond to input instructions and reach a stable state within the specified time. At the same time, the system should avoid generating excessive overshoot to reduce adverse effects on the actuator and the entire system.
2、 System reliability requirements
Strong overload capacity: Hydraulic servo systems should have strong overload capacity to cope with possible instantaneous overload or impact loads. Servo drives should typically be able to withstand an overload of 1.5 times or more within minutes or even half an hour without damage, and can withstand an overload of 4-6 times in a short period of time without damage.
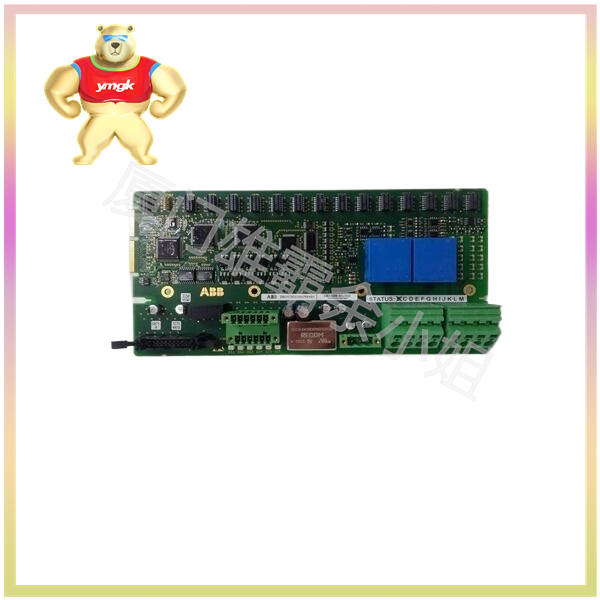
High reliability: The system should have high reliability and be able to operate stably in various harsh environments. This requires the system to have strong environmental adaptability such as temperature, humidity, vibration, and anti-interference ability.
Easy to maintain: The system should be designed to be easy to maintain and upkeep, in order to reduce downtime and repair costs. For example, the system should adopt a modular design to facilitate the replacement and maintenance of faulty components.
3、 Motor requirements
Smooth operation: The motor should be able to run smoothly from the lowest speed to the highest speed, with minimal torque fluctuations. Especially at low speeds, the motor should have no crawling phenomenon to ensure the stability and accuracy of the system.
High torque: The motor should have a large torque to meet the requirements of low-speed high torque. At the same time, the motor should have a large overload capacity to cope with possible instantaneous overload situations.
Fast response: In order to meet the requirements of fast response, the motor should have a small moment of inertia and a large locked rotor torque, and have the smallest possible time constant and starting voltage.
Frequent starting and braking capability: The motor should be able to withstand frequent starting, braking, and reversing operations to meet the needs of the system’s frequent changes in motion state.