Servo drive
(1) Definition and Function
A servo driver, also known as a “servo controller” or “servo amplifier”, is a type of controller specifically designed to control servo motors. Its function is similar to that of a frequency converter acting on a regular AC motor, and it is part of a servo system mainly used in high-precision positioning systems. The servo driver receives control signals (such as pulse signals or analog signals) and converts them into electrical signals to drive the servo motor, thereby achieving precise control of the servo motor.
(2) Composition and Working Principle
Servo drives typically consist of three parts: power supply, arithmetic unit, and power output. Among them, the power supply is responsible for providing stable electrical energy; The arithmetic unit is responsible for receiving control signals and processing them to generate electrical signals that drive servo motors; The power output part is responsible for converting electrical signals into the current or voltage required by the servo motor.
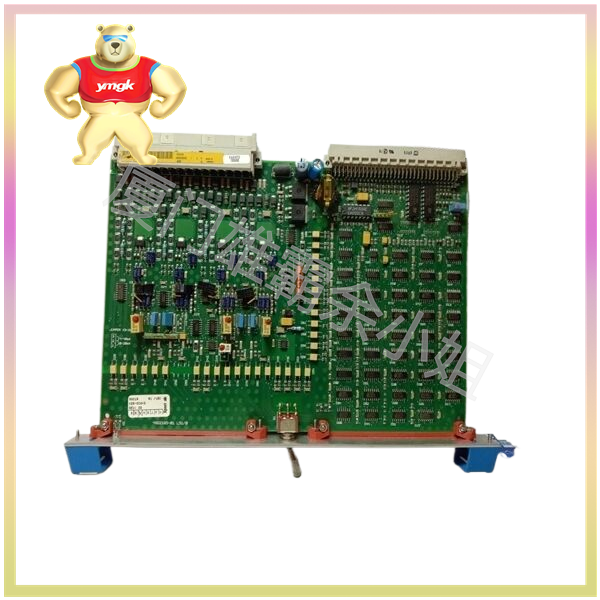
The mainstream servo drives use digital signal processors (DSPs) as the control core, which can implement complex control algorithms, achieve digitization, networking, and intelligence. Power devices commonly use driver circuits designed with intelligent power modules (IPMs) as the core, which have fault detection and protection circuits for overvoltage, overcurrent, overheating, undervoltage, etc., to ensure the stable operation of the driver.
(3) Application and technical characteristics
Servo drives are widely used in industrial robots, CNC machine tools, automation equipment, and other fields. Its main technical features include high-precision control, high dynamic response, safety and stability, and flexibility and adjustability. For example, by controlling the servo motor through position, speed, and torque, high-precision positioning of the transmission system can be achieved.