Hydraulic servo control system is a system that utilizes hydraulic transmission and servo control technology to achieve precise control. It is widely used in industries, aviation, shipbuilding, metallurgy, and other fields. This article will provide a detailed introduction to the control requirements of hydraulic servo control systems, including system composition, control principles, performance indicators, design points, and other aspects.
1、 System composition
The hydraulic servo control system mainly consists of the following parts:
Execution components: hydraulic cylinders, hydraulic motors, etc., used to convert hydraulic energy into mechanical energy and drive loads.
Control components: servo valves, proportional valves, etc., used to control the flow, pressure, and direction of hydraulic oil, achieving precise control of actuating components.
Sensors: displacement sensors, velocity sensors, pressure sensors, etc., used to detect the working status of the system and provide feedback signals to the controller.
Controller: PLC, IPC, etc., generate control instructions based on sensor signals and control algorithms, and drive control components to work.
Auxiliary components: oil tank, filter, cooler, etc., used to ensure the cleanliness, temperature and pressure stability of hydraulic oil.
2、 Control principle
The control principle of hydraulic servo control system mainly includes the following aspects:
Force control: By controlling the input pressure of the hydraulic cylinder, force control of the load is achieved.
Displacement control: By controlling the stroke of the hydraulic cylinder, displacement control of the load is achieved.
Speed control: By controlling the speed of the hydraulic motor, the speed control of the load is achieved.
Position control: By controlling the displacement of the hydraulic cylinder and the speed of the hydraulic motor, the position control of the load is achieved.
Pressure control: By controlling the pressure in the hydraulic system, stable control of the entire system is achieved.
3、 Performance indicators
The performance indicators of hydraulic servo control system mainly include the following aspects:
Accuracy: The control accuracy of the system, including force control accuracy, displacement control accuracy, velocity control accuracy, and position control accuracy.
Response speed: The system’s response time to control instructions, which affects the dynamic performance of the system.
Stability: The stability of the system under various operating conditions, including static stability and dynamic stability.
Load adaptability: The system’s ability to adapt to different loads, including adaptability to load changes and load fluctuations.
Anti interference capability: The system’s ability to resist external interference, including electromagnetic interference, vibration interference, etc.
4、 Design points
The design points of hydraulic servo control system mainly include the following aspects:
System selection: Select appropriate hydraulic and control components based on application scenarios and control requirements.
Control strategy: Design appropriate control strategies based on control objectives and system characteristics, such as PID control, fuzzy control, adaptive control, etc.
Control algorithm: Based on the control strategy, design specific control algorithms to achieve precise control of the system.
System integration: Organically integrate various components and control strategies together to form a complete hydraulic servo control system.
Parameter optimization: Through simulation and experimentation, optimize system parameters to improve system performance.
Reliability design: Consider the reliability of the system, design appropriate redundancy and protection measures to ensure the stable operation of the system.
Human computer interaction: Design a user-friendly interface for easy operation and monitoring of the system.
5、 Application Fields
Hydraulic servo control systems are widely used in the following fields:
Industrial automation: such as robots, CNC machine tools, injection molding machines, etc.
In the aviation field, such as aircraft control surfaces, landing gear control, etc.
Ship field: such as ship servo control, ship stability system, etc.
Metallurgical field: such as rolling mill control system, continuous casting machine control system, etc.
Energy sector: such as wind turbine control, hydroelectric generator control, etc.
6、 Development Trends
The development trend of hydraulic servo control system mainly includes the following aspects:
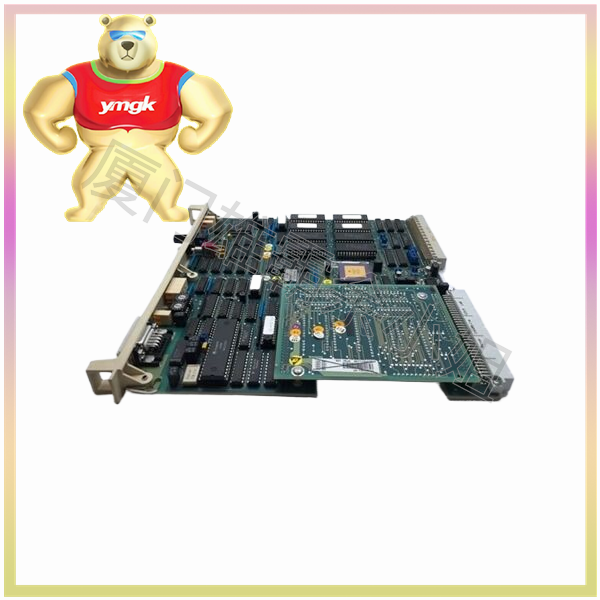
High performance: Improve the control accuracy, response speed, and stability of the system to meet higher requirements for application scenarios.
Intelligence: Introducing advanced control algorithms and artificial intelligence technology to achieve adaptive control and fault diagnosis of the system.
Integration: Highly integrate hydraulic components, control components, and sensors to reduce the volume and weight of the system.
Greening: Using environmentally friendly materials and energy-saving technologies to reduce the energy consumption and environmental impact of the system.
Networking: Achieve remote monitoring and control of the system, and improve the intelligence level of the system.
7、 Conclusion
As a high-precision, high response, and high stability control system, hydraulic servo control system has broad application prospects in industries such as aviation, shipbuilding, metallurgy, etc. With the continuous development of technology, hydraulic servo control systems will move towards high-performance, intelligent, integrated, green, and networked directions, providing better and more efficient control solutions for various industries.