The heating problem of the power module will seriously endanger the reliability of the module, causing the failure rate of the product to increase exponentially. What should be done if the power module heats up severely? High temperature has a significant impact on the reliability of power modules with high power density. High temperature can lead to reduced lifespan of electrolytic capacitors, decreased insulation properties of transformer enameled wires, transistor damage, material thermal aging, cracking and detachment of low melting point welds, and increased mechanical stress between devices.
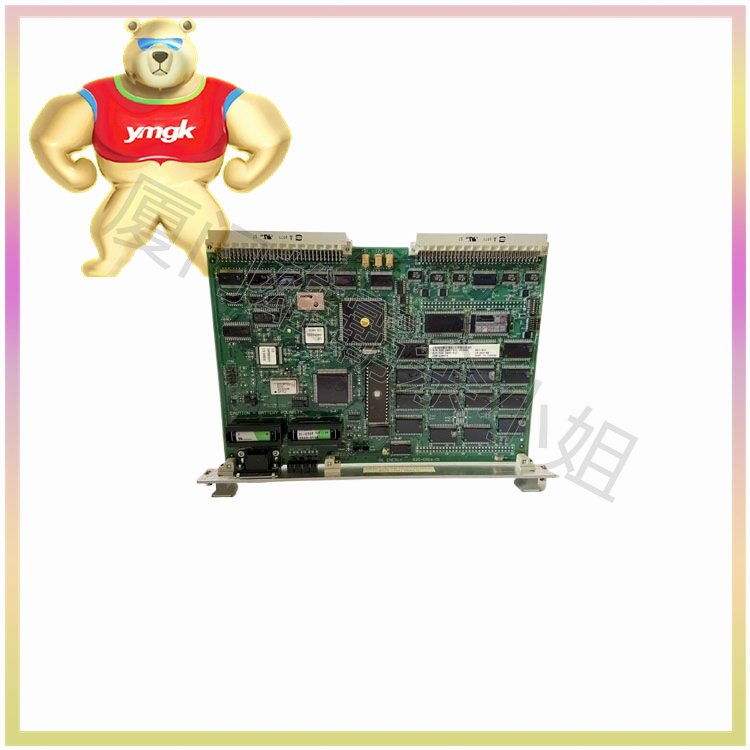
In many applications, the heat on the power module substrate needs to be conducted to distant heat dissipation surfaces through thermal conductive elements. In this way, the temperature of the power module substrate will be equal to the sum of the temperature of the heat dissipation surface, the temperature rise of the thermal conductive element, and the temperature rise of the two contact surfaces. The thermal resistance of a thermal conductive element is proportional to its length and inversely proportional to its cross-sectional area and thermal conductivity. Choosing appropriate thermal conductive materials and cross-sectional areas can also reduce the thermal resistance of the thermal conductive element.
Thermal conductive silicone gasket is an important factor affecting performance, and attention should be paid when selecting it. In most applications, the heat generated by the power module will be conducted from the substrate to the heat sink or thermal conductive element. However, a temperature difference will occur at the contact surface between the power module substrate and the thermal conductive element, which needs to be controlled. The thermal resistance is connected in series in the heat dissipation circuit, and the temperature of the substrate should be the sum of the temperature rise of the contact surface and the temperature of the thermal conductive element.
If not controlled, the temperature rise of the contact surface will be particularly significant. The contact surface area should be as large as possible. In order to eliminate surface roughness, thermal conductive silicone pads should be filled on the contact surface. After taking appropriate measures, the thermal resistance of the contact surface can be reduced.