PLC definition: A digitally operating electronic apparatus which uses a programming memory for the internal storage of instructions for implementing specific functions such as logic, sequencing, timing, counting and arithmetic to control through digital or analog modules, various types of machines or process.
DCS: DCS 50 is a control system in a production system, process or any type of dynamic system, in which element controllers are not centralized in one location, but are distributed to all systems with each sub-system component controlled by one or more controllers. The entire controller system is connected via a network for communication and monitoring.
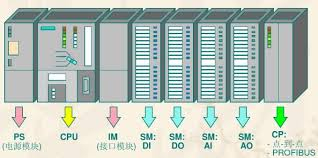
Difference between PLC and DCS:
DCS is a control system that works with several controllers, each controller will be designed to control separate plants. This each controller can be a PLC 51.
Basically we can say, PLC is a machine control system whereas DCS is for process control.
PLC is used Commonly with On\Off (Digital) Control and may be expanded with Analog I\O Modules for Analog Control and used for a unique task. It Controls the only machine on or off. DCS controls the many PLC’s at a time.
A PLC can be the subsystem of the DCS. The PLC dominates the control of the high-speed machine and the DCS prevail in complex continuous processes.
DCS has a wide range of communication, but PLC doesn’t have that much.
DCS is an automated distributed control that can provide instruction different part of the machine. PLC is a digital computer used for automation electromechanical processes.
PLC has to go offline to change any parameters. In DCS it can be done online.
Programming:
PLC programming is ladder logic, for DCS uses graphical function blocks that follow SAMA standards.
In DCS, it is easier to understand a boolean logic block diagram than a separate analog logic diagram and ladder logic diagram. For PLC its Challenge to write analog PID control using ladder logic.
PLC requires programmers to build the logical conditions and equations, it doesn’t have a standard algorithm. Besides having a standard library of algorithms such as PID, lead-lag, etc.,
Failure handling:
PLCs have relatively little diagnostic status and may only be indicative. It has limited use of diagnostic bits in logic.
DCS can diagnosis the instrument to the field level including HART and Fieldbus devices. DCS I/O is selectable either in HOLD-LAST or FAIL-SAFE positions in the event of failure.
PLCs are not support to work in remote areas, DCS cards have complete diagnostic and hot swap capability.