PLC (Programmable Logic Controller) is an electronic device used in automation control systems to monitor input signals and control outputs based on pre-set logic and algorithms. One important component is the analog module.
The analog module is an interface in the PLC system, used to convert analog signals into digital signals and input them into the PLC for processing. It can measure and convert various types of analog signals, such as temperature, pressure, flow rate, position, etc., and convert them into digital signals for PLC processing and operation.
Analog modules typically consist of multiple input channels, each of which can be connected to an analog sensor or signal generator. Sensors can convert measured physical quantities into electrical signals, which are then converted into digital signals through analog modules. This digital signal can be further processed and controlled to meet the requirements of automated control systems.
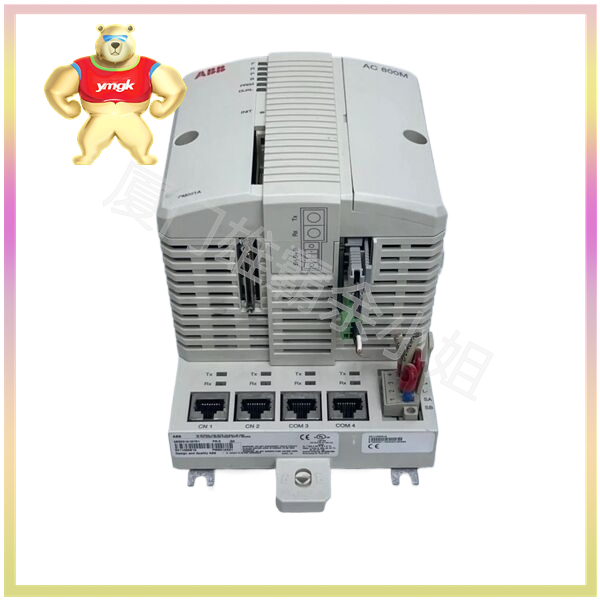
The use of analog modules in PLC requires following certain steps and procedures. Here is a simple guide to help you understand how to properly use the analog module of a PLC.
Determine the type and range of the input signal: Before using an analog module, you need to determine the type and range of the input signal, such as temperature range, pressure range, etc. This will help you choose the appropriate analog module and configure its parameters correctly.
Choose the appropriate analog module: Select the appropriate analog module based on the type and range of the input signal. Different modules are suitable for different types and ranges of analog signals. Usually, PLC suppliers will provide detailed product specifications to help you choose the most suitable module.
Connect analog sensors or signal generators: Connect sensors or signal generators to the input channels of analog modules. Ensure correct connections and follow the wiring diagram and guidelines provided by the supplier.
Configure analog module parameters: Use PLC programming software to configure the parameters of the analog module. These parameters include signal type, range, sampling rate, etc. By correctly configuring these parameters, analog signals can be converted to digital signals correctly.
Programming and Logic Control: Write logic control programs in PLC programming software. You can use logic blocks, function blocks, or other similar programming elements to define the processing logic and output control of input signals.
Testing and debugging: Before practical application, conduct testing and debugging to ensure the normal operation of the analog module. Use the analog signal input from the analog module and check if the PLC output meets expectations.
The use of analog modules in PLC can enable the application of various automation control systems. For example, real-time monitoring and control of temperature can be achieved through the use of temperature sensors and analog modules. By using pressure sensors and analog modules, pressure monitoring and control can be achieved.
In short, the analog module of PLC is an important component of implementing automation control systems. By correctly using analog modules, it is possible to measure, convert, and control analog signals.