In the frequency converter system, the input of numerical command signals is a crucial part, which includes key parameters such as frequency and voltage. These signals are divided into two types: digital input and analog input. Numerical input is usually set through keyboard operation or serial interface on the frequency converter panel; Analog input is provided by external devices through wiring terminals, and common input signals include voltage signals of 0-10V/5V or current signals of 0/4-20mA. Given the diversity of interface circuits, the input impedance of the frequency converter must be considered when selecting the output module of a PLC.
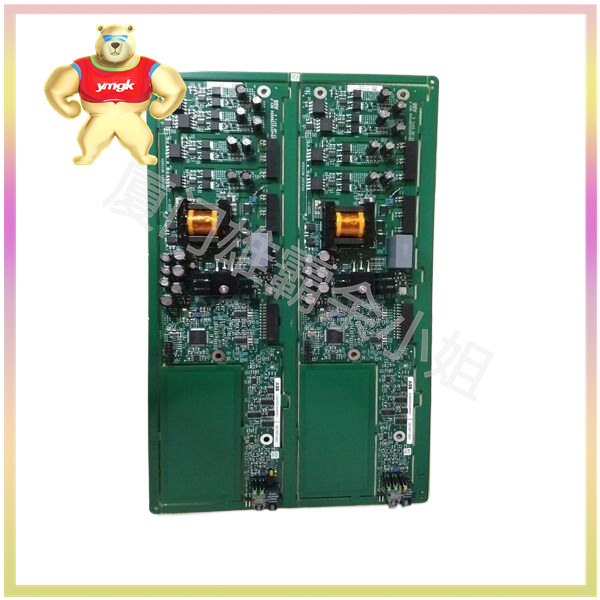
When the voltage signal range between the frequency converter and the PLC does not match, such as when the input signal of the frequency converter is 0-10V and the output voltage signal range of the PLC is 0-5V, or vice versa, it is necessary to use current limiting resistors and voltage dividers to ensure that the signal transmission process does not exceed the capacity limits of both devices. In addition, noise interference from the main circuit side should be avoided during wiring to ensure clear and accurate signal transmission.
Frequency converters usually output analog signals for monitoring purposes to the outside through wiring terminals, which may range from 0 to 10V/5V or 0/4 to 20mA current signals. In any case, it should be ensured that the input impedance on the PLC side is sufficiently large to avoid voltage and current exceeding the allowable values in the circuit, which is related to the reliability and accuracy of the entire system. If you have any questions about the configuration of the monitoring system, you should consult the manufacturer.
When using PLC for sequential control, the time required for CPU to process data should be taken into account, which may result in some time delay. Therefore, this factor must be considered when precise control is needed.
Due to the strong electromagnetic interference generated by the frequency converter during operation, the following points should be noted when connecting the frequency converter to the PLC to reduce interference:
Properly ground the PLC and avoid sharing the grounding wire with the frequency converter, ensuring that the grounding points of the two are separated as much as possible.
When the power quality is poor, noise filters and noise reduction transformers should be installed on the power lines of the PLC’s power module and input/output module.
If the frequency converter and PLC are installed in the same operating cabinet, the wires related to both should be separated as much as possible.