(1) The hardware function of PLC is switch control, which is the basic function of PLC. For switch control system, it is mainly necessary to consider whether the maximum switch I/O points of PLC can meet the requirements of the system.
Some systems have special requirements for the functions of PLC, such as communication networking, PID closed-loop control, fast response, high-speed counting, and motion control. Modular PLC should consider whether there are corresponding special functional modules. The integrated PLC generally includes functions such as high-speed counter, high-speed pulse output, analog adjustment potentiometer, pulse capture, real-time clock, and interrupt function.
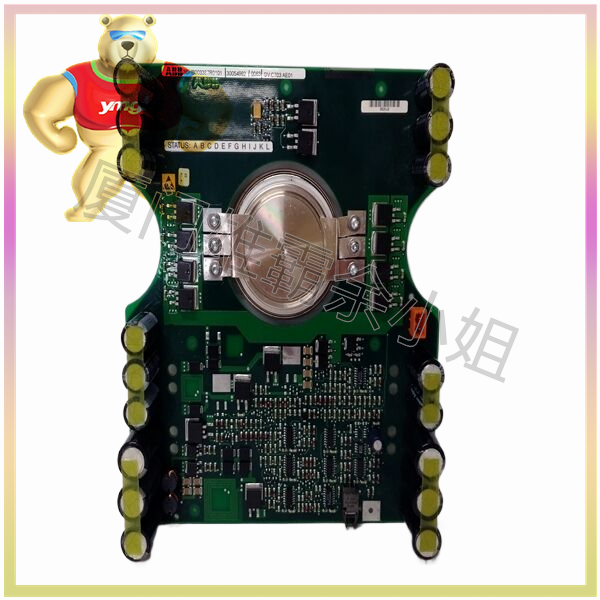
For systems that require analog control, it is necessary to consider whether the maximum number of analog I/O points can meet the system’s requirements, the number of points per module, and the average price per point. Some small systems may require a module with both analog input and output to meet the requirements, which can save hardware costs. Some PLCs
(2) The function of the PLC instruction system is sufficient for small single devices that only require switch control, and a typical small PLC can meet the requirements. If the system requires the PLC to perform certain special functions, consideration should be given to whether the PLC’s instruction system has corresponding instructions to support them. In addition, it should be considered whether the programming components of the PLC (such as auxiliary relays, timers, counters, data registers, etc.) are sufficient, but generally they are sufficient.
(3) The user memory capacity of PLC is sufficient for general systems, but in some special cases, this issue may need to be considered. The memory capacity is related to the model of the CPU module, and some PLCs allow the use of memory cards to increase the user memory capacity.
(4) The response time of PLC refers to the total time it takes to convert the corresponding external input into a given output, which includes the delay time of input filters, I/O service delay time, logic solution time, and delay time of output components. The delay caused by the scanning working mode can reach 2-3 scanning cycles.
PLC manufacturers generally provide the delay time of input and output circuits, as well as the average speed of executing basic logic instructions (in ms/K words). Some manufacturers also provide the time required to execute each instruction. When running the user program, the scanning cycle can be read using programming software.
(5) The selection of physical structure for PLC: The average price per I/O point for integrated PLC is cheaper than modular PLC, and integrated PLC is generally used in small control systems. However, the functional expansion of modular PLCs is convenient and flexible. There is much more room for choice in terms of the number of I/O points, the ratio of input points to output points, the type and number of I/O modules, and the use of special I/O modules compared to integrated PLCs. It is also convenient to replace modules and determine the scope of faults during maintenance. Therefore, more complex and demanding systems generally choose modular PLCs.
(6) To determine the number of stolen input points for selecting the model and number of I/O modules, it is necessary to determine which signals need to be input to the PLC, which loads are driven by the PLC, whether they are switch or analog, DC or AC, and the voltage level; Are there any special requirements, such as quick response, etc.? The number of points should be classified and counted. If different parts of the system are far apart, remote I/O can be considered.
(7) If the PLC needs to communicate with other devices or be integrated into the factory control network, the communication networking function of the PLC needs to be considered, such as what kind of communication interfaces the PLC has, how many interfaces can be configured at most, what communication protocols can be used, communication speed, and maximum communication distance.
(8) For systems with extremely high reliability requirements, consideration should be given to whether the PLC has redundant functions and whether it can form a redundant control system.
When choosing a PLC model, one should not blindly pursue excessively high performance indicators. There should be a certain margin in terms of I/O points and memory capacity, with a general margin of 10% for I/O points.