DCS (Distributed Control System) is a control system used for industrial automation, consisting of multiple control nodes distributed throughout the entire factory or facility. DCS systems are typically used to handle complex control tasks such as process control, monitoring, and data acquisition. DCS systems have high flexibility, scalability, and reliability.
PLC (Programmable Logic Controller) is an electronic device used in industrial automation, mainly for implementing functions such as sequential control, logic control, and timing control. PLC has the advantages of high reliability, easy programming, and maintenance.
Now let’s explore whether DCS can achieve all the functions of PLC.
control function
DCS and PLC can both achieve control functions, but they differ in their implementation methods. DCS usually adopts a centralized control architecture, while PLC adopts a distributed control architecture. In some cases, DCS can replace PLC to achieve control functions, but this depends on the specific application scenario and requirements.
Programming and Logic Functions
The main advantage of PLC lies in its programming and logic functions. PLCs use programming languages such as ladder diagrams, functional block diagrams, and sequential functional diagrams, which are easy to understand and program. DCS systems typically use high-level programming languages such as C, C++, or Python, which require higher programming skills. In some cases, DCS can implement programming and logic functions of PLC, but this may require additional development work and costs.
Communication and data exchange
Both DCS and PLC can achieve communication and data exchange functions. DCS systems typically have stronger communication capabilities and can support multiple communication protocols and interfaces. The communication capability of PLC may be limited, especially when processing large amounts of data. In some cases, DCS can achieve communication and data exchange functions of PLC, but this depends on the specific system architecture and requirements.
Human Machine Interface (HMI)
Both DCS and PLC can implement human-machine interface (HMI) functions. DCS systems typically have more advanced HMI functions, such as real-time data monitoring, historical data recording, and alarm management. The HMI function of PLC may be relatively simple, mainly used for displaying and controlling basic control parameters. In some cases, DCS can implement the HMI function of PLC, but this may require additional development work and costs.
Scalability and flexibility
The DCS system has high scalability and flexibility, and can be expanded and upgraded according to actual needs. The scalability and flexibility of PLC may be limited, especially when dealing with complex control tasks. In some cases, DCS can achieve the scalability and flexibility of PLC, but this depends on the specific system architecture and requirements.
Reliability and Maintenance
Both DCS and PLC have the characteristics of high reliability and easy maintenance. However, DCS systems typically have higher reliability because they adopt a distributed architecture and redundant design. The reliability of PLC may be limited, especially when dealing with complex control tasks. In some cases, DCS can achieve the reliability and maintenance functions of PLC, but this depends on the specific system architecture and requirements.
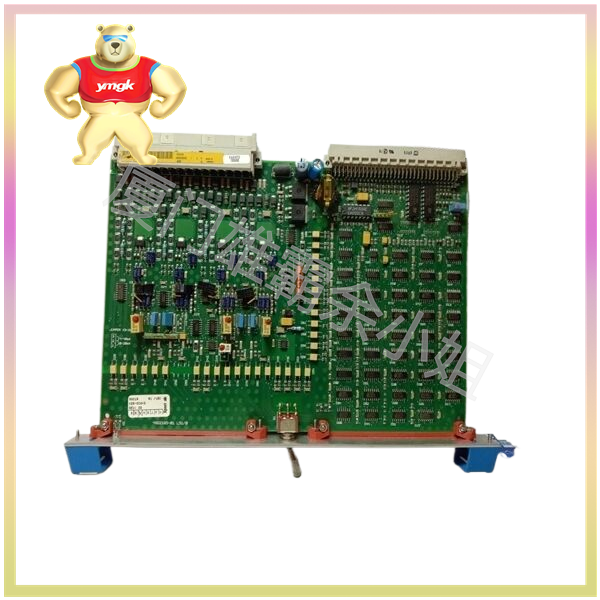
Cost and return on investment
The cost of DCS systems is usually higher than that of PLC systems, especially in the initial investment and development stages. However, DCS systems can provide higher performance, reliability, and scalability, which may lead to higher investment returns. In some cases, DCS can achieve the cost and return on investment of PLC, but this depends on the specific application scenario and requirements.
Summary:
DCS and PLC have similar functions in many aspects, but there are differences in implementation, performance, and cost. In some cases, DCS can achieve all the functions of PLC, but this depends on the specific application scenario, requirements, and system architecture. When choosing DCS or PLC, it is necessary to weigh the actual needs, budget, and expected return on investment.