1、 Definition
PLC control (Programmable Logic Controller): PLC is a digital operating electronic system specifically designed for industrial automation. It uses programmable memory to store instructions for performing logical operations, sequential control, timing, counting, and arithmetic operations, and controls various types of mechanical or production processes through digital or analog input/output.
Distributed Control System (DCS): DCS is a highly integrated and modular control system that distributes control functions throughout the entire factory or production process. DCS is usually composed of multiple control nodes, which are connected through a network to achieve data sharing and collaborative control.
2、 Composition
Composition of PLC control:
a. Central Processing Unit (CPU): responsible for executing programs and processing data.
b. Input/Output (I/O) module: used to receive external signals and control external devices.
c. Power module: Provides stable power supply for the PLC system.
d. Communication module: Implement communication between PLC and other devices or systems.
e. Human Machine Interface (HMI): Used for displaying and controlling PLC systems.
Composition of DCS control:
a. Control Nodes: Responsible for executing control algorithms and processing data.
b. Input/Output (I/O) Station: Used to receive external signals and control external devices.
c. Communication network: enables data transmission between controllers, I/O stations, and other devices.
d. Operator Stations: Used for displaying and controlling DCS systems.
e. Engineer Stations: Used for configuring, diagnosing, and maintaining DCS systems.
3、 Application scenarios
Application scenarios of PLC control:
a. Sequential control: such as packaging machinery, assembly lines, etc.
b. Logical control: such as traffic signal lights, elevator control, etc.
c. Motion control: such as conveyor belts, robots, etc.
d. Process control: control of parameters such as temperature, pressure, flow rate, etc.
Application scenarios of DCS control:
a. Petrochemical industry: such as refining, petrochemicals, fertilizers, etc.
b. Electricity: such as thermal power generation, hydropower generation, nuclear power, etc.
c. Metallurgy: such as steel, non-ferrous metals, etc.
d. Food and beverage: such as beverage production lines, food processing, etc.
4、 Advantages and disadvantages
Advantages and disadvantages of PLC control:
a. Advantages:
i. Simple structure, easy to install and maintain.
Ii. Suitable for industrial automation projects of various scales.
Iii. Has high reliability and stability.
Iv. Programming is relatively simple, easy to learn and use.
b. Disadvantages:
i. The control function is relatively limited, making it difficult to implement complex control algorithms.
Ii. Poor scalability and difficulty in adapting to large-scale control systems.
Iii. Weak data sharing and collaborative control capabilities.
Advantages and disadvantages of DCS control:
a. Advantages:
i. Powerful control function, capable of implementing complex control algorithms.
Ii. Good scalability and easy adaptation to control systems of different scales.
Iii. Strong data sharing and collaborative control capabilities are beneficial for improving production efficiency.
Iv. It has highly integrated monitoring and diagnostic functions, making it easy to maintain and manage.
b. Disadvantages:
i. The structure is complex, and the installation and maintenance costs are high.
Ii. For small projects, there may be issues with excessive design.
Iii. Programming and configuration are relatively complex and require professional technical personnel.
5、 Development Trends
The development trend of PLC control:
a. Integrate more advanced features such as motion control, communication, etc.
b. Improve data processing capabilities and real-time performance.
c. Strengthen integration with other systems such as MES, ERP, etc.
d. Develop open architecture to improve system compatibility and scalability.
The development trend of DCS control:
a. Adopting more advanced control algorithms to improve control accuracy and stability.
b. Strengthen integration with other systems to achieve comprehensive optimization of the production process.
c. Develop technologies such as cloud computing and big data to enhance data processing and analysis capabilities.
d. Improve the reliability and security of the system, and reduce maintenance costs.
6、 Summary
PLC control and DCS control have wide applications in the field of industrial automation. They each have different characteristics and advantages, suitable for different application scenarios. With the continuous development of technology, both PLC and DCS are moving towards higher levels, integration, and intelligence, bringing more possibilities to the field of industrial automation.
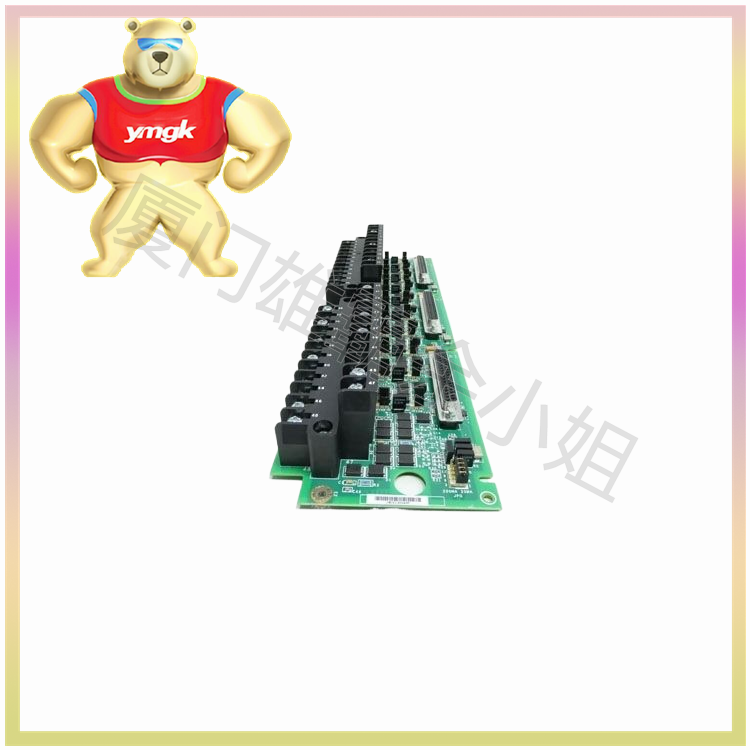