Principle of stepper relay
Stepper relay, also known as stepper bistable relay or stepper self-locking relay, is a relay driven by pulse current and maintained by mechanical structure with self-locking contacts. It can be driven by AC or DC voltage.
A stepper relay consists of a coil, an armature, a push rod, a ratchet, a pawl, and contacts. Its ratchet has three layers, with the middle layer performing a stepping motion. When a current is applied to the coil, it generates a magnetic field, which causes the armature to be attracted towards the iron core under the action of electromagnetic attraction. At this time, the armature drives the push rod to rotate the middle ratchet counterclockwise by one step, and the upper and lower layers of ratchet move the plate spring. Due to the fact that the contacts are fixed to the leaf spring, the movement of the leaf spring will cause the upper and lower layers of contacts to change their contact state. After the driving pulse disappears, the coil loses current and the electromagnetic force also disappears. The armature returns to its initial state under the action of the restoring spring. At this time, the pawl presses against the tooth surface of the ratchet wheel to prevent it from rotating, playing a positioning role. Therefore, the contact point can maintain its state unchanged.
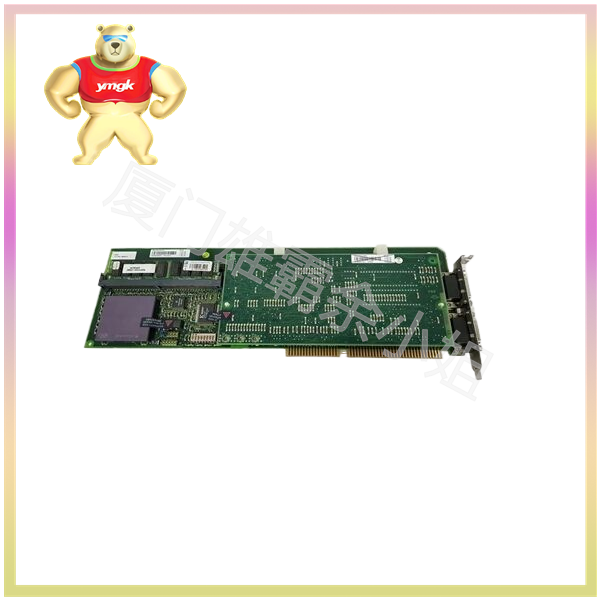
Characteristics of stepper relay
(1) The circuit is simple and energy-saving. Stepper relays can be directly driven by AC power without the need for additional DC circuits, simplifying electronic circuits. Stepper relays do not require maintaining current and are driven by pulse current, requiring very little electrical energy and saving energy.
(2) Safe and reliable. Due to the fact that stepper relays do not require maintaining current, they can fundamentally eliminate their own safety hazards.
(3) Strong control function, convenient and flexible application. A stepper motor can have 1-2 contacts and multiple step sequences, equivalent to a simple program controller with strong control capabilities. It is also very convenient and flexible when applied, and can be freely expanded in terms of usage scope.
The detection method of stepper relay
- Measure contact resistance
Using the resistance range of the multimeter, measure the resistance between the normally closed contact and the moving point. The resistance value should be 0 (using a more accurate method, the contact resistance value can be measured within 100 milliohms); The resistance between the normally open contact and the moving point is infinite. From this, we can distinguish which one is a normally closed contact and which one is a normally open contact. - Measure coil resistance
The resistance of the relay coil can be measured using a multimeter in the R × 10 Ω range to determine if there is an open circuit in the coil. - Measure the pull in voltage and pull in current
Find an adjustable voltage regulator and ammeter, input a set of voltage to the relay, and connect the ammeter in series in the power supply circuit for monitoring. Slowly increase the power supply voltage, and when you hear the sound of the relay closing, record the closing voltage and current. For accuracy, you can try multiple times and calculate the average. - Measure the release voltage and release current
Similarly to the above connection test, when the relay is pulled in, gradually reduce the power supply voltage. When you hear the relay release sound again, record the voltage and current at this time. You can also try multiple times to obtain the average release voltage and current. In general, the release voltage of a relay is about 10-50% of the pull in voltage. If the release voltage is too small (less than 1/10 of the pull in voltage), it cannot be used normally, which will pose a threat to the stability of the circuit and result in unreliable operation.