The working principle of a thermal relay is that the current entering the thermal element generates heat, causing deformation of bimetallic sheets with different expansion coefficients. When the deformation reaches a certain distance, it pushes the connecting rod to open the control circuit, causing the contactor to lose power and the main circuit to disconnect, achieving overload protection for the motor.
In actual operation, such as driving production machinery, if there are abnormal mechanical conditions or circuit abnormalities that cause the motor to experience overload, the motor speed will decrease, the current in the winding will increase, and the temperature of the motor winding will rise. If the overload current is not large and the overload time is short, and the motor winding does not exceed the allowable temperature rise, this overload is allowed. But if the overload time is long and the overload current is high, the temperature rise of the motor winding will exceed the allowable value, causing the motor winding to age, shortening the service life of the motor, and in severe cases, even causing the motor winding to burn out. So, this kind of overload is something that the electric motor cannot withstand. Thermal relay is a protective electrical device that uses the principle of thermal effect of current to cut off the motor circuit and provide overload protection for the motor when it cannot withstand overload.
When using a thermal relay for overload protection of an electric motor, connect the thermal element in series with the stator winding of the motor, connect the normally closed contact of the thermal relay in series with the control circuit of the electromagnetic coil of the AC contactor, and adjust the setting current adjustment knob to keep the herringbone lever and push rod at an appropriate distance. When the motor is working normally, the current passing through the heating element is the rated current of the motor. The heating element heats up, and the bimetallic strip bends after being heated, causing the push rod to just make contact with the herringbone lever but unable to push the herringbone lever. The normally closed contacts are in a closed state, the AC contactor remains engaged, and the motor operates normally.
If the motor is overloaded, the current in the winding increases, and the current in the thermal relay element increases, causing the temperature of the bimetallic strip to rise higher and the degree of bending to increase. This pushes the herringbone lever, which in turn pushes the normally closed contacts, causing the contacts to disconnect and the AC contactor coil circuit to be disconnected. This releases the contactor, cuts off the power supply to the motor, and the motor stops for protection.
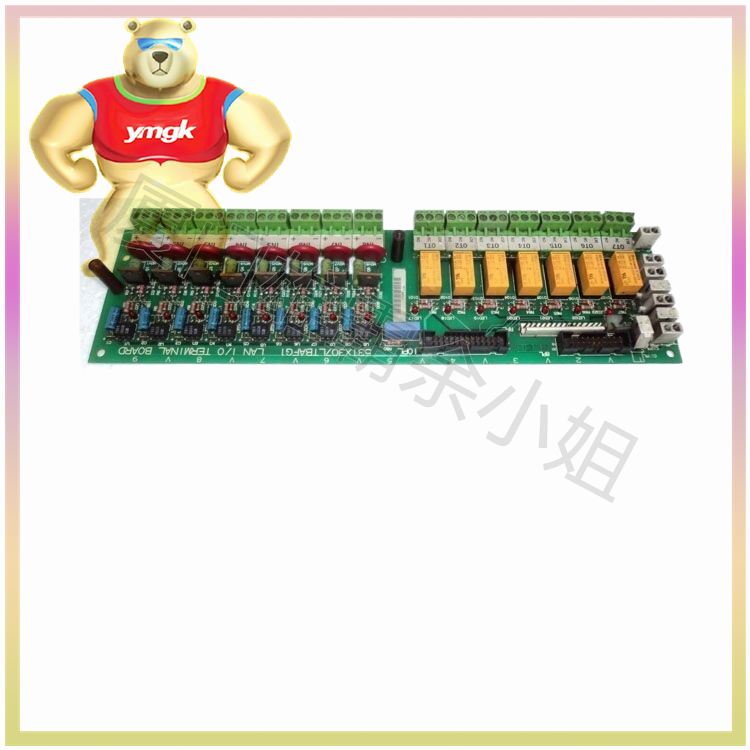
The function of other parts of the thermal relay is as follows: the left arm of the herringbone lever is also made of bimetallic sheet. When the ambient temperature changes, the bimetallic sheet in the main circuit will deform and bend to a certain extent. At this time, the left arm of the herringbone lever will also deform and bend in the same direction, so that the distance between the herringbone lever and the push rod remains basically unchanged, ensuring the accuracy of the thermal relay action. This effect is called temperature compensation.
Screw 8 is a normally closed contact reset adjustment screw. When the screw position is to the left, the normally closed contact will disconnect after the motor is overloaded. After the motor stops, the bimetallic strip of the thermal relay will cool down and reset. The moving contact of the normally closed contact will automatically reset under the action of the spring. At this time, the thermal relay is in automatic reset state. When the screw is rotated counterclockwise to the right and adjusted to a certain position, if the motor is overloaded at this time, the normally closed contact of the thermal relay will disconnect. The moving contact will swing to a new equilibrium position on the right side. After the motor is powered off and stopped, the moving contact cannot be reset. The reset button must be pressed before the moving contact can be reset. At this time, the thermal relay is in manual reset state. If the motor overload is a fault, in order to avoid easily starting the motor again, the thermal relay should be reset manually. To switch the thermal relay from manual reset mode to automatic reset mode, simply turn the reset adjustment screw clockwise to the appropriate position.