The working principle of the motor controller mainly includes the following steps:
Input signal processing: The motor controller first receives external control signals, such as switch signals, analog signals, etc. The input interface converts these signals into a format suitable for processing by the control unit.
Control strategy execution: The control unit calculates the operating parameters of the motor, such as speed, torque, etc., based on the input signal and preset control strategy. The control strategy can be PID control, fuzzy control, neural network control, etc.
Drive signal generation: The control unit converts the calculated motor operating parameters into drive signals and outputs them to the motor through the drive circuit. The driving signal can be a PWM signal, an analog voltage signal, etc.
Motor drive: The drive circuit receives the drive signal output by the control unit and converts it into voltage and current signals suitable for motor drive. These signals drive the motor to operate through drivers such as frequency converters, servo drives, etc.
Feedback signal acquisition: The motor controller collects the operating status of the motor, such as speed, torque, current, etc., through sensors such as encoders and current sensors. These feedback signals are used for closed-loop control of the control unit.
Protection function execution: When an abnormal situation occurs in the motor or controller, the protection circuit will immediately start, cut off the power supply to the motor, and protect the motor and controller from damage.
Communication and Display: The motor controller exchanges data with other devices through communication interfaces, such as uploading operational data and receiving control instructions. At the same time, the display and operation interface of the controller can display the operating status and parameters of the motor, making it convenient for users to operate and monitor.
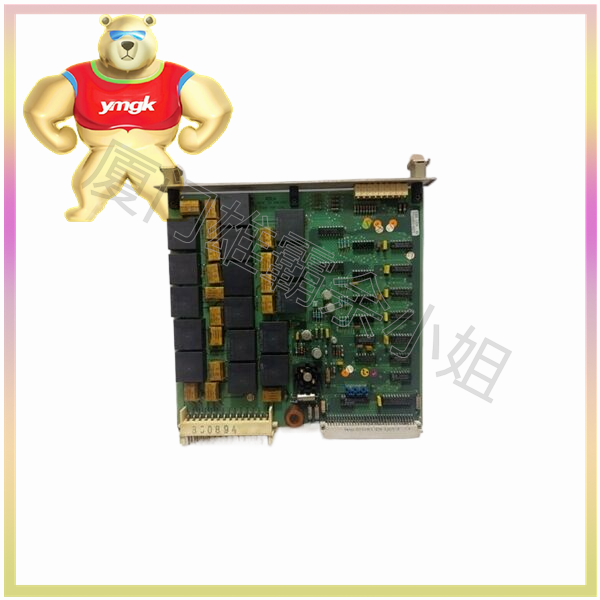