Function and application scenarios
PID controller: mainly used for controlling continuously changing analog quantities, such as temperature, pressure, flow rate, etc. It achieves precise control of the controlled object by adjusting the parameters of the proportional, integral, and derivative stages. The PID controller is suitable for systems with essentially linear and dynamic characteristics that do not vary over time.
PLC: has a wider range of functions and application scenarios. In addition to basic logic control, PLC can also achieve functions such as timing, counting, arithmetic operations, and can be programmed to accomplish complex automation control tasks. PLC is widely used in industrial production lines, robot control, automotive electronic control systems, medical equipment and other fields.
control mode
PID controller: adopts feedback control to adjust the input value by continuously comparing the error between the system output and the reference value, so that the system output gradually approaches the reference value. The control algorithm of PID controller is relatively simple and direct, suitable for precise control of a single variable.
PLC: Using programming control, corresponding control programs can be written according to different application scenarios and requirements. PLC can achieve complex logical operations and data processing functions, suitable for controlling and coordinating multiple variables.
cost
PID controller: usually has a lower cost because its main function is relatively simple and its structure is straightforward. PID controllers are suitable for precise control of a single variable, such as temperature control, flow control, etc.
PLC: The cost is relatively high because its functions are more complex and it has stronger data processing and logical computing capabilities. However, the flexibility and scalability of PLC make it more cost-effective in complex automation control systems.
flexibility
PID controller: Although it can adapt to different application scenarios by adjusting parameters, its function is relatively fixed and lacks flexibility. Once the application scenario changes or new control functions need to be added, it may be necessary to replace or modify the PID controller.
PLC: It has high flexibility and scalability. Users can write or modify control programs according to their actual needs to achieve different control functions. In addition, PLC can communicate and coordinate with other devices and systems to achieve more complex automation control tasks.
Maintenance and Upgrade
PID controller: Due to its simple structure and fixed function, maintenance and upgrading are relatively simple. Usually, it is only necessary to check whether the circuit connections and parameter settings are correct.
PLC: Due to its complex software and hardware structure, maintenance and upgrading are relatively difficult. Professional technicians are required for fault diagnosis and program modification. However, the programming and debugging tools of PLC make these tasks easier and more efficient.
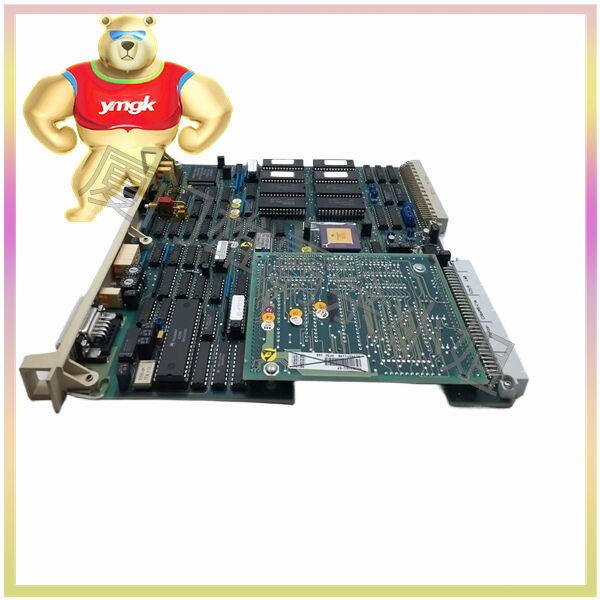
5、 Conclusion
In summary, there are significant differences between PID controllers and PLCs in terms of functionality, application scenarios, control methods, cost, flexibility, and maintenance upgrades. PID controllers are suitable for precise control of a single variable, while PLCs have a wider range of functions and application scenarios, making them suitable for complex automation control systems. When choosing which controller to use, it is necessary to evaluate and select based on specific application requirements and scenarios.