ID controller, also known as proportional integral derivative controller, is a widely used automatic control regulator. It consists of a proportional unit (P), an integral unit (I), and a differential unit (D), and achieves precise control of the controlled object by adjusting the parameters (Kp, Ki, Kd) of these three units. PID controllers are mainly suitable for systems that are essentially linear and have dynamic characteristics that do not change over time, such as temperature, pressure, flow, and other control scenarios.
The working principle of a PID controller is to collect system data and compare it with a reference value, calculate a new input value based on the error signal, and adjust the system output to reach or maintain the reference value. Compared with other simple control algorithms, PID controllers can adjust input values based on historical data and the rate of error change, making the system more accurate and stable.
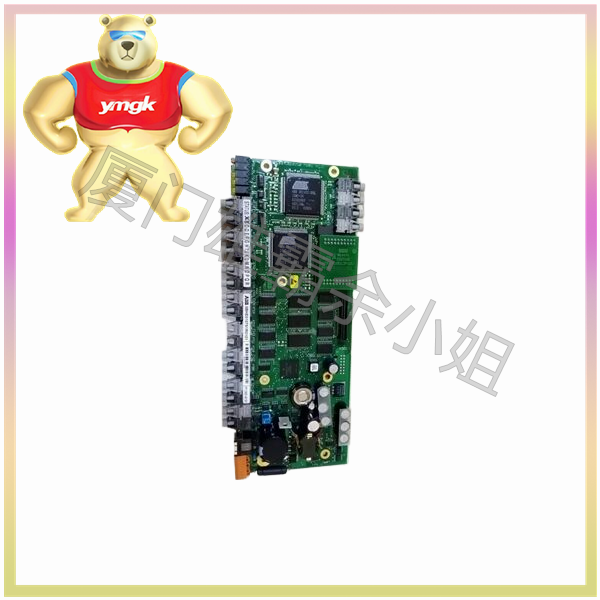
3、 Overview of PLC
PLC, The full name is Programmable Logic Controller, which is a digital operation electronic system designed specifically for industrial environments. It uses programmable memory to store instructions for performing logical operations, sequential control, timing, counting, and arithmetic operations, and controls various types of mechanical equipment or production processes through digital or analog input and output.
PLC consists of functional units such as CPU, instruction and data memory, input/output interfaces, power supply, etc., and has powerful data processing and logical operation capabilities. It can achieve complex automation control tasks through programming and is widely used in industrial production lines, robot control, automotive electronic control systems, medical equipment, and other fields.