Plc excels in logic control, such as implementing circuit logic control. It belongs to high-voltage equipment and is mainly used to control the start and stop of motors. Dcs is good at analog control and belongs to weak equipment, mainly used for analog control of liquid level, flow rate, and temperature. (Beginners can learn by combining PLC video tutorials)
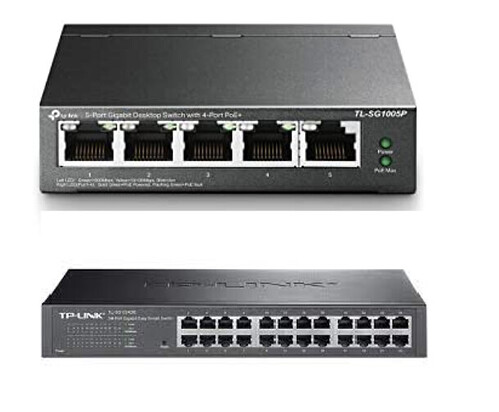
Programmable controllers and distributed control systems were initially developed by two types of technicians who faced different control objects. PLC is mainly targeted at automobile manufacturing, with little or no analog quantity. Developers are mainly electrical technicians who use computer logic operations instead of relay logic. Later, DCS was introduced to the market and developed by the original instrument technicians. It replaces the original analog operation with computer simulation operation based on the operational amplifier.
The research content of the two is different. DCS was first applied in petrochemical systems, and later both wanted to capture the market. PLC has increased the operation of analog quantities, while DCS has developed logical operations. However, both have some defects in the newly developed parts. The simulation calculation function blocks developed by PLC are few, the programming is complex, and the price is relatively expensive. The cost of each circuit is about $2300, and the logic operation developed by DCS takes tens of milliseconds to complete a NAND gate operation, while PLC only takes a fraction of a millisecond.
In terms of maintenance, DCS has high maintenance costs and strict requirements for grounding resistance. Modules are often burned out due to insufficient grounding resistance. PLC does not require strict grounding resistance, so maintenance costs are relatively low.
Therefore, if there are many analog quantities, advanced control schemes such as expert systems, model control, DCS, etc. are needed. If there are many switches, it is recommended to use a PLC.