There are three main ways in which PLC controls servo drives: torque control, position control, and speed control.
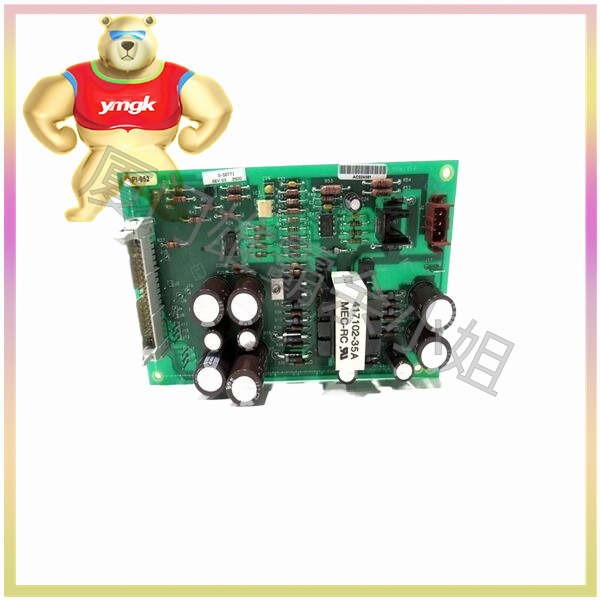
Torque control
The torque control method is to set the output torque of the motor shaft to the outside through external analog input or direct address assignment. Specifically, PLC can send torque set values to servo drivers through analog output modules, and servo drivers control the output torque of servo motors based on these set values. The torque control method is suitable for situations that require precise control of output torque, such as material handling, tension control, etc.
position control
The position control mode generally determines the speed of rotation by the frequency of external input pulses, and determines the angle of rotation by the number of pulses. PLC can send pulse signals to servo drivers through high-speed pulse output modules, and servo drivers control the position and speed of servo motors based on these signals. The position control mode is suitable for situations that require precise positioning and speed control, such as machine tool processing, robot control, etc.
speed control
The speed control mode controls the rotational speed through analog input or pulse frequency. PLC can send speed setting values to servo drivers through analog output modules or high-speed pulse output modules, and servo drivers control the operating speed of servo motors based on this setting value. The speed control mode is suitable for situations that require continuous speed adjustment, such as conveyor belts, mixers, etc.