How to adjust the servo controller
The debugging of servo controllers requires specific settings and adjustments based on specific application scenarios and controller models. Generally speaking, the debugging of servo controllers includes the following aspects:
Electrical parameter adjustment: including motor parameter setting and calibration, driver parameter setting, power output adjustment, etc. The settings of these parameters need to be adjusted according to the specific controller manual and application scenarios.
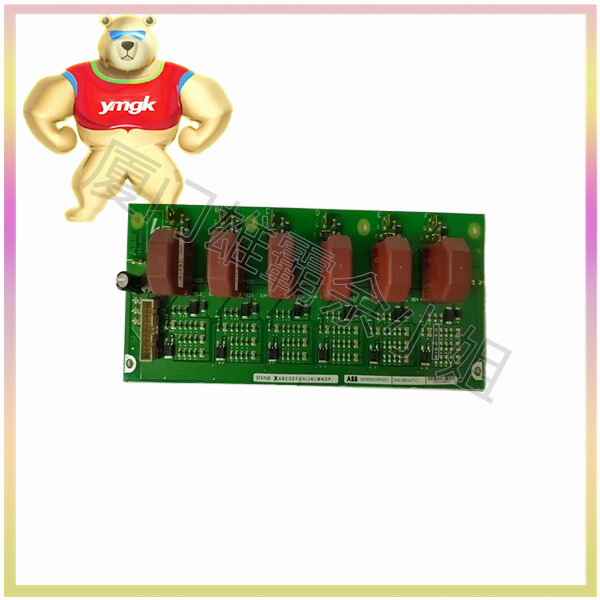
Control mode selection: Servo controllers usually have multiple control modes to choose from, such as position control mode, speed control mode, torque control mode, etc., which need to be selected according to the actual application scenario.
PID parameter adjustment: Servo controllers usually use PID control algorithms, and PID parameter settings and adjustments need to be made according to actual application scenarios to achieve better control performance.
Adjustment of motion parameters: including the setting and adjustment of motion parameters such as acceleration, deceleration, and maximum speed, which need to be adjusted according to actual application scenarios.
Troubleshooting: During the debugging process, various faults may occur, such as electrical faults, control faults, etc., which need to be promptly resolved.
In short, the debugging of servo controllers requires specific settings and adjustments based on the specific application scenario and controller model. It is recommended to carefully read the controller manual before debugging and set and adjust according to the requirements of the manual. At the same time, safety should be taken into account during debugging to avoid causing harm to personnel and equipment.
The difference between servo controller and servo driver
Servo controllers and servo drivers are two different devices, and their roles and functions are also different.
A servo drive is a device that controls the speed and output torque of a motor. It is mainly responsible for converting control signals from a servo controller into motor control signals, achieving precise control of the motor. Servo drives typically use PWM modulation technology, which can convert DC voltage into AC signals with variable frequency and amplitude, thereby achieving precise control of motor speed and torque.
A servo controller is a device that controls servo drives and motors. It is mainly responsible for monitoring and controlling parameters such as position, speed, acceleration, torque, etc. of the motor, and achieves precise control of the motor through cooperation with the servo drive. Servo controllers typically use PID control algorithms, which can adjust the control signal of the motor based on feedback signals, thereby achieving precise control of the motor.
Therefore, servo controllers and servo drives play different roles in the control system, and their roles and functions are to cooperate with each other to achieve precise control of the motor.