Microcontrollers are also used for specific applications in the automation industry that have their advantages. However, they have some limitations that make PLCs more popular in many automation scenarios:
cost
Microcontrollers are usually more cost-effective than PLCs and are suitable for budget conscious projects or applications with simpler control requirements.
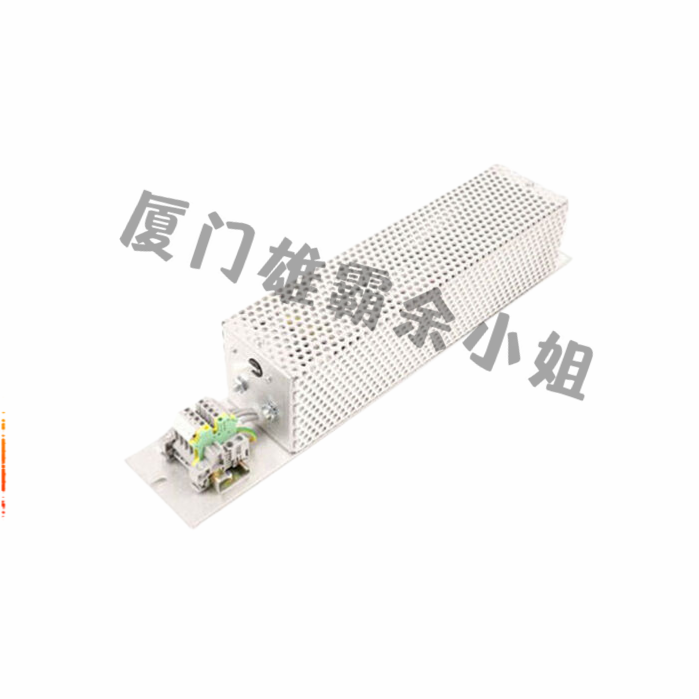
small-scale
Microcontrollers are typically used in small or independent systems where control and monitoring tasks are relatively simple and do not require a large amount of I/O or complex logic.
customized
Microcontrollers provide more customization options, allowing developers to customize hardware and software according to specific application needs, which is very advantageous for niche projects.
Embedded system
Microcontrollers are commonly used in embedded systems, where control functions are directly integrated into devices such as household appliances, consumer electronics, and automotive systems.
real-time performance
Some microcontrollers have been optimized for real-time control and can efficiently handle time sensitive tasks. However, this usually depends on the specific microcontroller and its functionality.
low power consumption
The microcontroller is designed for low-power operation, suitable for battery powered and energy-saving applications.
Rapid prototyping
Microcontrollers are widely popular in rapid prototyping and development due to their simple and fast setup, allowing engineers to test ideas and concepts before large-scale implementation.
Custom logic and algorithms
Microcontrollers enable developers to implement custom control algorithms and logic, which may not be as simple in PLCs.
Despite these advantages, microcontrollers still have some limitations compared to PLCs, which is why PLCs are favored in many automation industries:
Reliability and robustness
PLC is designed to operate in harsh industrial environments and can withstand temperature changes, humidity, electrical noise, and vibration. They are manufactured using industrial grade components and have higher reliability and longer lifespan compared to microcontrollers.
Real time operation
PLC has been optimized specifically for real-time control and monitoring tasks. They have dedicated hardware and firmware that can quickly and accurately execute logic, making them an ideal choice for time critical automation processes.
I/O Scalability
PLC provides various input/output (I/O) modules that can be easily expanded and expanded to meet different automation needs. This flexibility makes it suitable for both small and large industrial applications.
Standardization
PLC follows industry standards such as IEC 61131-3 and can provide a unified programming environment. This standardization ensures compatibility, consistency, and ease of programming between different PLC brands and models.
User friendly programming
PLC programming is typically done using ladder logic or other graphical programming languages, which are easier for control engineers and technicians to understand and maintain. This simplicity helps to shorten learning time and accelerate the development speed of automated applications.
Built in communication protocol
PLC comes with built-in communication protocols such as Modbus, Profibus, Ethernet/IP, etc., which can be seamlessly integrated with other industrial equipment such as human-machine interface (HMI), SCADA system, and distributed control system (DCS).
Security function
PLCs typically include built-in safety features such as watchdog timers, redundancy, and secure memory storage. These security measures are crucial for ensuring the reliable and safe operation of critical automation systems.