distributed control system
DCS is the most commonly used control architecture in industrial process control
DCS can be defined as an architecture where subsystems are geographically distributed but functionally integrated. DCS is the most cost-effective and scalable solution, suitable for small factories to large refineries.
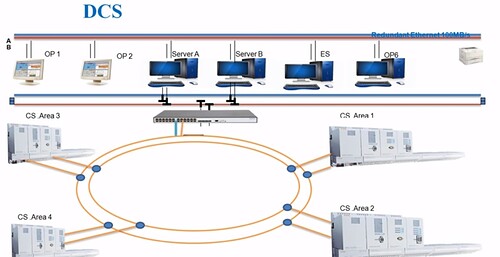
distributed control system
distributed control system
1677×862 144 KB
Components of DCS
The typical subsystems of DCS are operator stations, engineer stations, process control networks, controllers, and I/O modules.
Operator Station
The operator station can visually view the process and easily access process graphics, panels, alarm summaries, alarm panels, trends, and display navigation. The operator station has expanded from traditional process monitoring and control to diagnosis. Diagnosis includes monitoring intelligent devices, mechanical monitoring, and network monitoring to increase process uptime and reduce unplanned downtime.
Operation Station
Operation Station
1048×607 134 KB
Engineering Station
Engineering stations can flexibly implement systems to meet project and process requirements. With the emergence of process design and control requirements, engineers can dynamically implement various parts of the system in a modular manner. As process requirements become clear in agile mode, engineering can be carried out in stages. Engineers only need to put in minimal effort to specify control circuits and on-site equipment, and then quickly complete the configuration.
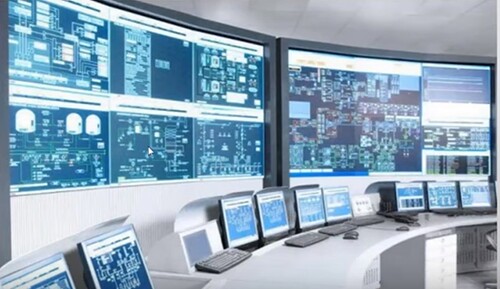
Process Control Network
The backbone network connecting the entire DCS in the process control network. The network runs through the entire factory, connecting all smart devices in a reliable and deterministic manner. Process control networks (also known as PCNs) can be open protocols (such as Ethernet) or proprietary protocols. PCN is usually installed in redundant monitors to improve reliability, and is installed away from conventional power lines to reduce the impact of electromagnetic interference, thereby improving the reliability of the entire system.
controller
The controller executes control strategies to assist in optimizing the process. The controller has redundant and non redundant configurations. The execution speed of control strategy determines the quality of control. The controller is equipped with a rich library that can be used for various algorithms such as PID, cascade, feedforward, etc. The controller receives input from the input module channel connected to it. Similarly, the controller sends the output to the configuration channel of the output module to drive the final control component.
I/O module
I/O module is a modular subsystem designed for installation near instruments on site. I/O modules participate in the network to communicate with the controller. I/O modules can also serve as gateways for communication with intelligent field devices through fieldbus networks. I/O modules can also be configured as redundancy in critical control circuits.
I/O module
I/O module
985×522 89.5 KB
Advantages of DCS
The overall availability is higher because a single controller failure will not cause the entire automation system to fail.
Each controller has a small volume, making operation and troubleshooting relatively convenient.
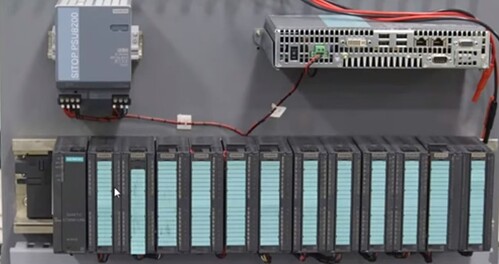