Communication module to enhance communication between PLC and I/O
The main function of the PLC communication module is to establish a synchronization protocol with other devices, exchange and share data in the PLC system with data in other control devices, and control, monitor and collect relevant data, that is, to monitor each other through mutual monitoring instructions, thus achieving the purpose of production coordination.
There are fieldbus modules, industrial Ethernet modules, and wireless communication modules here, divided according to different protocols. The commonly used protocols currently include Ethernet/IP, EtherCAT, Modbus, DeviceNet, RS232/RS422/RS485, and so on. The current communication module design usually needs to consider many aspects, such as being able to be used for the expansion of multi protocol industrial Ethernet, increasing flexibility, which is now highly valued, and also requiring enhanced protection against coupling noise in harsh environments. At the same time, the demand for diagnostic functions is also evident, such as the widely used Ethernet cable diagnostic function.
Time sensitive TSN communication is a technology that has the potential to replace buses, and PLC is a typical application of it. Relying on its significantly improved certainty, TSN has obvious advantages in addressing latency and jitter. Real time communication interfaces such as Profinet and EtherCAT enable precise time sensitive communication between PLCs and input/output modules. These interfaces can adjust the TAS extension and frame first mechanism, enabling the use of standard TSN hardware for industrial Ethernet. These industrial Ethernet protocols benefit from this, and communication between PLCs and I/O modules is faster and more accurate with these enhanced features.
Compact I/O modules in PLC
In previous PLC systems, I/O modules were generally designed as sub modules under CPU modules, but now the trend is that more and more PLC devices are separating I/O modules. The I/O module is used to obtain signals from on-site sensors and control actuators, while the communication module adapter is used to expand local or remote I/O.
Under the serial connection of communication protocols, I/O modules connect various sensors/actuators and PLCs/adapters on site, and define various digital input/output, analog input/output, and sensor signals in the I/O module. And now the density of I/O modules is getting higher and higher, with hundreds of I/O modules in an industrial scenario. In the case of a significant increase in density, the reliability and durability of I/O modules are crucial.
Taking the inputs of temperature, pressure, flow rate, liquid level, gas, and other sensors and detectors in industrial scenarios as an example, these inputs require analog input modules to digitize the analog information received from the field, and then transmit the digitized information to the CPU module of the PLC. Such a compact input module inevitably requires isolation, interrupting the grounding loop between the on-site sensor and CPU module, otherwise communication will be disrupted.
When these high-density modules are combined, the possibility of electromagnetic interference is greatly increased, and temperature rise problems are more likely to occur. Therefore, while I/O modules are developing towards compactness, the design difficulty is also greatly increased.
Therefore, I/O modules are constantly introducing new diagnostic functions, from basic diagnosis to module diagnosis, and then to channel diagnosis. The diagnostic level of I/O modules is also constantly improving, ensuring that I/O modules are reliable enough under compact and high-density conditions. Many scenarios that require high performance from PLCs now require I/O modules to provide support for functions such as oversampling, PWM, and integrated counting.
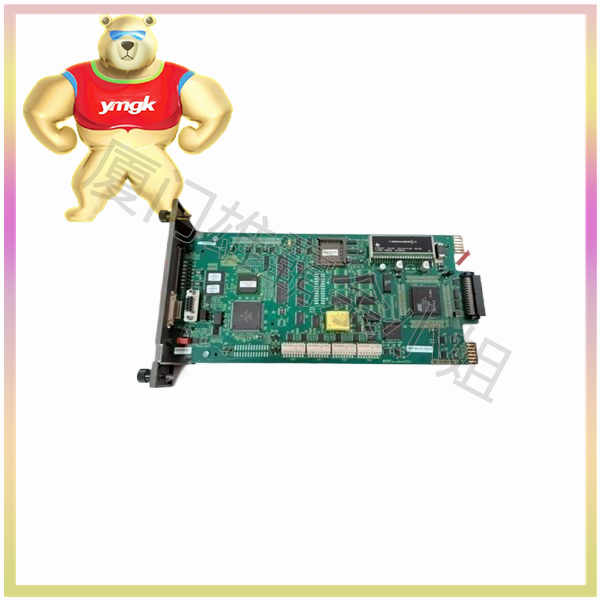