The industrial robot control system mainly consists of the following parts:
Controller: The controller is the core of the industrial robot control system, responsible for receiving input signals, processing information, and generating control instructions. Controllers typically use high-performance computers or embedded systems.
Sensors: Sensors are used to detect the status and environmental information of robots, such as position, velocity, acceleration, force, temperature, etc. The data from sensors can be used for real-time monitoring, fault diagnosis, and adaptive control.
Driver: The driver is responsible for converting the control instructions of the controller into the motion of the robot actuator. Drivers usually use servo motors or hydraulic systems.
Executor: An actuator is the end effector of a robot, responsible for completing various operational tasks such as handling, assembly, welding, spraying, etc.
Communication interface: The communication interface is used to connect and exchange data between the robot control system and other devices or systems, such as PLC, CNC, MES, etc.
Human computer interaction interface: The human computer interaction interface is used to enable interaction between operators and robot control systems, such as programming, debugging, monitoring, etc.
2、 Function
The industrial robot control system has the following main functions:
Motion control: Motion control is the basic function of industrial robot control systems, including linear motion, circular motion, compound motion, etc.
Path planning: Path planning is the automatic generation of a robot’s motion trajectory based on task requirements and the robot’s workspace.
Speed control: Speed control is the real-time adjustment of the robot’s motion speed based on task requirements and the robot’s motion state.
Acceleration control: Acceleration control is the real-time adjustment of the robot’s motion acceleration based on task requirements and the robot’s motion state.
Force control: Force control is the real-time adjustment of the robot’s force output based on task requirements and force sensor data.
Visual control: Visual control is achieved through the robot’s visual system to recognize, locate, and track objects.
Adaptive control: Adaptive control is the automatic adjustment of control strategies based on the real-time status and environmental information of robots to adapt to different tasks and environments.
Fault diagnosis: Fault diagnosis is achieved by monitoring the status and performance of robots in real-time, and promptly detecting and handling faults.
Security protection: Security protection ensures the safe operation of robots by monitoring their movements and environment in real-time.
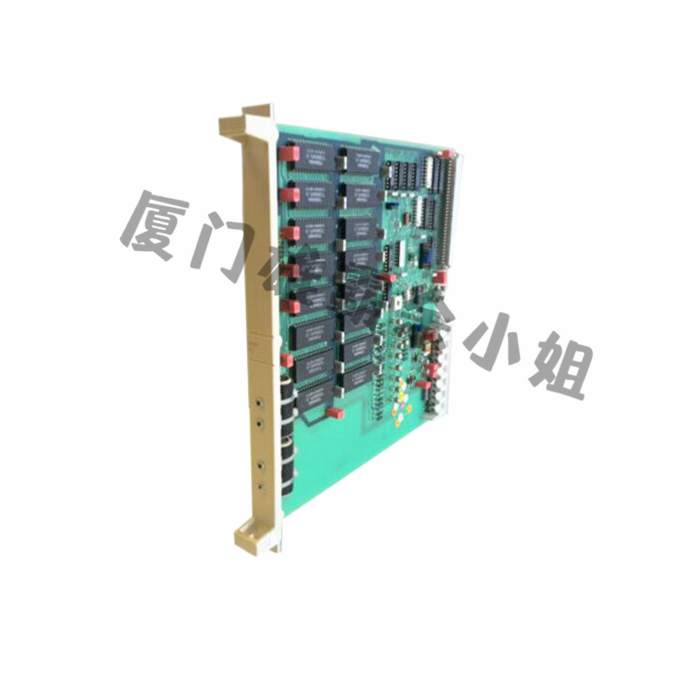
3、 Performance
The performance of industrial robot control systems mainly includes the following aspects:
Accuracy: Accuracy is an important indicator of industrial robot control systems, including position accuracy, velocity accuracy, acceleration accuracy, etc.
Stability: Stability is the ability of industrial robot control systems to maintain stable operation under various working conditions.
Response speed: Response speed is the speed at which industrial robot control systems respond to input signals, which affects the efficiency of the robot’s work.
Real time performance: Real time performance refers to the ability of industrial robot control systems to meet real-time requirements during real-time monitoring and control processes.
Reliability: Reliability is the ability of industrial robot control systems to maintain normal operation over long periods of time.
Anti interference capability: Anti interference capability refers to the ability of industrial robot control systems to maintain normal operation under various interference conditions.
4、 Reliability
The reliability of industrial robot control system is the key to its normal operation. Measures to improve reliability include:
Hardware redundancy: By increasing the redundancy of hardware, the fault tolerance of the system can be improved.
Software Fault Tolerance: By designing fault-tolerant software, the system’s fault tolerance capability can be improved.
Fault diagnosis: Through real-time monitoring and fault diagnosis, timely detection and handling of faults.
Maintenance: Extend the service life of the system through regular maintenance.
Environmental adaptability: By improving the environmental adaptability of the system, the impact of the environment on the system can be reduced.
5、 Flexibility
The flexibility of industrial robot control systems lies in their ability to adapt to different tasks and environments. Measures to improve flexibility include:
Modular design: Through modular design, the system can be quickly upgraded and expanded.
Parameterized programming: Through parameterized programming, tasks can be quickly configured and adjusted.
Adaptive control: Through adaptive control, adaptability to different tasks and environments can be achieved.
Multi tasking: By multitasking, multiple tasks can be executed simultaneously.
Human computer interaction: Through human-computer interaction, operators can quickly interact with the system.
6、 Intelligentization
The intelligence of industrial robot control systems is its development trend. Intelligent measures include:
Artificial Intelligence: Through artificial intelligence technology, robots can achieve autonomous decision-making and learning.
Big data analysis: Through big data analysis, optimize and improve robots.
Cloud computing: Through cloud computing, remote control and collaborative work of robots can be achieved.
Internet of Things: Through IoT technology, robots can achieve interconnectivity with other devices.
Virtual Reality: Using virtual reality technology to simulate and train robots.