Basic concepts of PLC
PLC is an electronic system designed specifically for industrial automation, which uses a programmable memory to store programs internally, execute user oriented instructions such as logical operations, sequential control, timing, counting, and arithmetic operations, and control various types of mechanical equipment or production processes through digital or analog input/output. A PLC consists of a central processing unit (CPU), memory, input/output (I/O) interfaces, power supply, and communication interfaces.
3、 PLC programming tool
PLC programming tools are the key to implementing automation control logic. There are currently various PLC programming software on the market, such as Omron PLC programming software CX One, Siemens STEP 7, Mitsubishi GX Works, etc. These software provide rich programming languages and tools, such as ladder diagrams, structured text, etc., to facilitate users in program design and development.
4、 The Implementation Method of PLC Automation Control Logic
requirement analysis
Before implementing PLC automation control logic, it is necessary to conduct a detailed analysis of the control requirements. This includes determining the control object, control requirements, input and output signals, etc. For example, on a production line, it may be necessary to control the actions of multiple motors, cylinders, and other actuators through PLC to achieve automatic assembly and testing of products.
Program Design
Based on the results of the requirements analysis, use PLC programming software for program design. In the process of programming, it is necessary to choose a suitable programming language (such as ladder diagrams, structured text, etc.) and write corresponding programs according to control requirements. In program design, attention should be paid to the correctness of logical relationships, the stability and maintainability of the program, and other aspects.
Program debugging
After the program is written, debugging is required to ensure its correctness and stability. During the debugging process, simulation software or actual equipment can be used for testing. During the debugging process, it is necessary to check the functionality of each logical module one by one, and troubleshoot and repair any problems that arise.
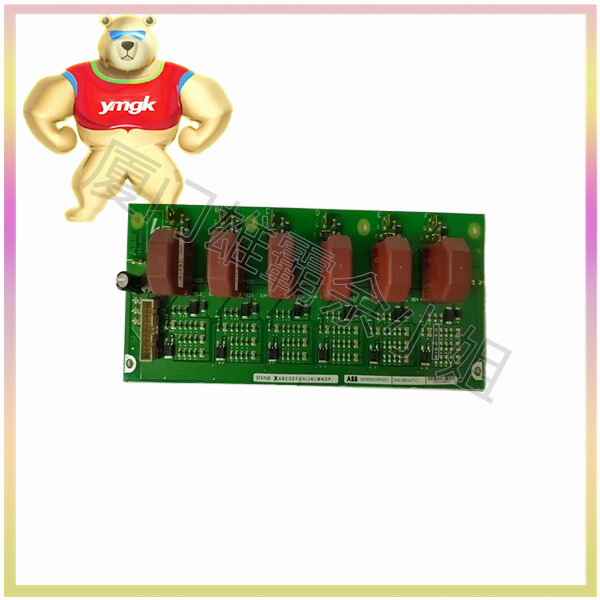
On site installation and debugging
After the program debugging is completed, it is necessary to install the PLC on the actual production site and conduct on-site debugging. During the on-site debugging process, it is necessary to check whether the connection between the PLC and the on-site equipment is correct, and whether the communication is normal. At the same time, further optimization and adjustment of the PLC program are needed to meet the actual production needs.
5、 Practical application cases
Here is a simple example of implementing PLC automation control logic:
A certain production line requires automatic assembly and testing of products. On this production line, there is a motor used to drive the conveyor belt to transport products to designated positions, and another cylinder used to remove products from the conveyor belt and place them on the inspection table. To achieve this function, PLC can be used for control.
requirement analysis
Control objects: motors and cylinders;
Control requirements: After the motor is started, it drives the conveyor belt to transport the product to the designated position. The cylinder action removes the product from the conveyor belt and places it on the inspection table;
Input and output signals: motor start signal, motor stop signal, cylinder extension signal, cylinder retraction signal, etc.
Program Design
Use ladder diagram programming language for program design. Firstly, draw the control logic diagram of the motor and cylinder, and then write the corresponding ladder diagram program based on the control logic diagram. In the program, it is necessary to set an appropriate delay time to ensure the correct sequence of actions for the motor and cylinder.
Program debugging
Use simulation software for program debugging. During the debugging process, check the functionality of each logical module one by one, and troubleshoot and fix any problems that arise.
On site installation and debugging
Install the PLC onto the actual production site and conduct on-site debugging. Check whether the connection between PLC, motor and cylinder is correct, and whether communication is normal. At the same time, further optimization and adjustment of the PLC program should be carried out to meet the actual production needs.
6、 Summary
This article provides a detailed introduction to the implementation method of PLC automation control logic, including steps such as requirement analysis, program design, program debugging, and on-site installation and debugging. By selecting appropriate PLC programming tools and programming languages, and combining them with practical needs for program design and debugging, complex automation control logic can be achieved. In practical applications, flexible adjustments and optimizations need to be made according to specific situations to ensure the stability and reliability of PLC systems.