The main functions of robot controllers
The robot controller is an important component of a robot, used to control the manipulator to complete specific work tasks. Its basic functions are as follows.
- Memory function: stores job sequence, motion path, motion mode, motion speed, and information related to production process.
- Teaching function: offline programming, online teaching, indirect teaching. Online teaching includes two types: teaching box and guided teaching.
- Communication with peripheral devices: input and output interfaces, communication interfaces, network interfaces, synchronization interfaces.
- Coordinate setting function: There are four coordinate systems: joint, absolute, tool, and user-defined.
- Human machine interface: teaching box, operation panel, display screen.
- Sensor interface: position detection, vision, touch, force perception, etc.
- Position servo function: robot multi axis linkage, motion control, speed and acceleration control, dynamic compensation, etc.
- Fault diagnosis and safety protection function: monitoring the system status during operation, safety protection under fault conditions, and fault self diagnosis.
What are the problems with robot controllers
With the rapid development of modern science and technology and the progress of society, higher requirements have been put forward for the performance of robots. The research on intelligent robot technology has become a major development direction in the field of robotics, such as various precision assembly robots, position hybrid control robots, multi limb coordination control systems, and robots in advanced manufacturing systems. Correspondingly, higher requirements have been put forward for the performance of robot controllers. However, since the birth of robots, especially the controllers used in industrial robots, have mostly been developed by developers based on their own independent structures, using dedicated computers, dedicated robot languages, dedicated operating systems, and dedicated microprocessors. This type of robot controller can no longer meet the requirements of modern industrial development.
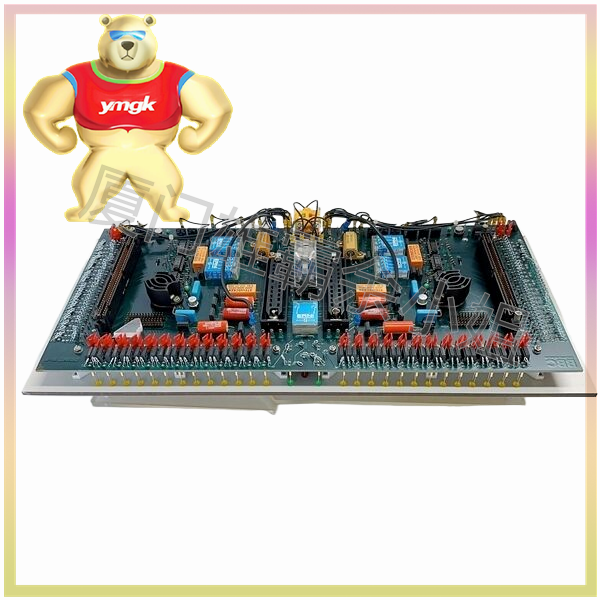
Overall, there are many problems with existing robot controllers, such as:
(1) Poor openness is limited to the closed structure of “dedicated computers, dedicated robot languages, and dedicated microprocessors”. The closed controller structure gives it specific functions and adaptability to specific environments, making it difficult to expand and improve the system.
(2) The software independence is poor, and the software structure and its logical structure depend on the processor hardware, making it difficult to transplant between different systems.
(3) Poor fault tolerance: Due to the inherent characteristics of data correlation, communication, and synchronization in parallel computing, the fault tolerance performance of the controller deteriorates, and a failure of one processor may lead to the paralysis of the entire system.
(4) Poor scalability currently. The research on robot controllers focuses on improving and enhancing system performance at the joint level. Due to the closed structure, it is difficult to expand the system as needed, such as adding functional modules such as sensor control.
Overall, both serial and parallel robot controllers mentioned earlier are not open architectures, and are difficult to expand and modify in terms of software and hardware. For example, the controller of the commercial Mo Toman robot is not open, and users find it difficult to modify and expand its functions according to their own needs. The usual approach is to dissect and analyze it in detail, and then modify it.