Servo motor is a high-precision, high response speed motor widely used in industrial automation, robotics, aerospace and other fields. There are many control methods for servo motors, and here we will introduce the simplest and most basic control method – open-loop control.
Open loop control is a control system without feedback loop. Its working principle is to directly transmit input signals to the actuator, and control the system through the response of the actuator. In open-loop control of servo motors, the input signal is usually a pulse signal, and the control of motor speed and torque is achieved by controlling the frequency and duty cycle of the pulse.
The following is a detailed, detailed, and meticulous introduction to open-loop control of servo motors:
Basic principles of servo motors
A servo motor is a device that converts electrical signals into mechanical motion. It is mainly composed of stator, rotor, encoder, driver and other parts. The working principle of a servo motor is to use the principle of electromagnetic induction to generate a rotating magnetic field by changing the current in the stator winding, thereby driving the rotor to rotate.
Servo motors have the characteristics of high precision, high response speed, large torque, and low inertia, making them widely applicable in various scenarios.
1.1 Classification of servo motors
Servo motors can be divided into two categories based on their structure and working principle: DC servo motors and AC servo motors.
1.1.1 DC servo motor
DC servo motor is mainly composed of armature, commutator, stator, brush holder and other parts. Its working principle is to use DC power supply to control the motor speed and torque by changing the magnitude and direction of the armature current.
1.1.2 AC servo motor
The communication servo motor is mainly composed of stator, rotor, encoder, driver and other parts. Its working principle is to use AC power supply to control the motor speed and torque by changing the frequency and phase of the current in the stator winding.
1.2 Characteristics of servo motors
Servo motors have the following characteristics:
1.2.1 High precision
Servo motors have high-precision control performance and can achieve precise control of parameters such as motor speed, torque, and position.
1.2.2 High response speed
Servo motors have high response speed and can achieve fast start, stop, and acceleration/deceleration.
1.2.3 High torque
Servo motors have a large torque output, which can meet the needs of various loads.
1.2.4 Low inertia
Servo motors have low rotational inertia and can achieve fast dynamic response.
1.2.5 Good control performance
Servo motors have good control performance and can implement various complex control strategies.
Open loop control of servo motor
Open loop control is a control system without feedback loop. Its working principle is to directly transmit input signals to the actuator, and control the system through the response of the actuator.
2.1 Basic principles of open-loop control
In open-loop control of servo motors, the input signal is usually a pulse signal. By controlling the frequency and duty cycle of the pulses, the control of motor speed and torque can be achieved.
2.1.1 Pulse frequency control
Pulse frequency refers to the number of pulses generated per unit time. In open-loop control of servo motors, the pulse frequency is proportional to the motor speed. By changing the pulse frequency, the control of motor speed can be achieved.
2.1.2 Pulse duty cycle control
Pulse duty cycle refers to the proportion of time that a high level occupies within a pulse cycle. In open-loop control of servo motors, the pulse duty cycle is proportional to the torque of the motor. By changing the pulse duty cycle, the control of motor torque can be achieved.
2.2 Advantages of open-loop control
Open loop control has the following advantages:
2.2.1 Simple Structure
The structure of open-loop control system is simple, easy to implement and maintain.
2.2.2 Low cost
Due to the simple structure of open-loop control systems, their cost is relatively low.
2.2.3 Convenient Implementation
The implementation of open-loop control systems is relatively convenient and can be achieved through simple hardware and software.
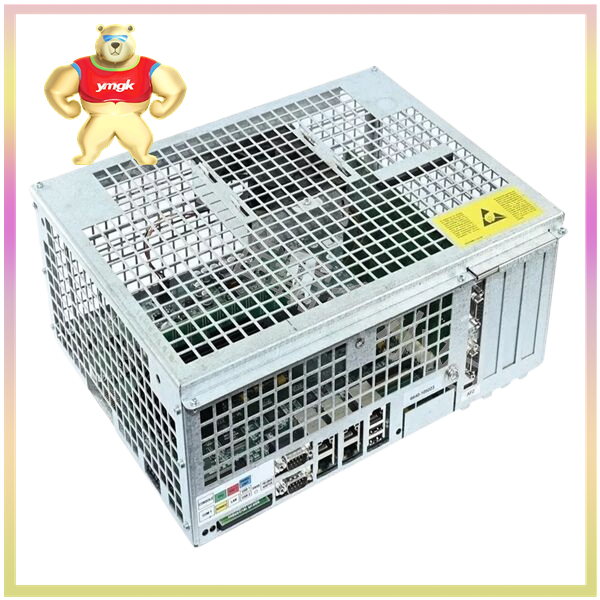
2.3 Disadvantages of open-loop control
Open loop control also has the following drawbacks:
2.3.1 Low control accuracy
Due to the lack of feedback loop in open-loop control system, its control accuracy is relatively low.
2.3.2 Poor anti-interference ability
Open loop control systems have poor resistance to external interference and are easily affected by external environments.
2.3.3 Poor system stability
The stability of open-loop control systems is relatively poor, and it is prone to system oscillation and instability.
Implementation method of open-loop control
3.1 Hardware Implementation
The hardware implementation of open-loop control mainly includes pulse signal generator, driver, servo motor and other parts.
3.1.1 Pulse Signal Generator
The pulse signal generator is the core component of an open-loop control system, responsible for generating control pulse signals. The pulse signal generator can be implemented using hardware such as microcontroller, PLC, FPGA, etc.