Classification of servo control systems
Servo control systems can be classified from multiple perspectives, and the following are some common classification methods:
Classified by control quantity
(1) Position servo control system: mainly used for precise control of the position of objects. By comparing the actual position of the object with the set value, a position error signal is generated. The controller adjusts the output of the actuator based on the error signal to achieve the predetermined position of the object. The position servo control system is widely used in fields such as CNC machine tools, robots, printing equipment, etc.
(2) Speed servo control system: mainly used for precise control of the motion speed of objects. By comparing the actual speed of the object with the set value, a speed error signal is generated. The controller adjusts the output of the actuator based on the error signal to make the object move at the desired speed. The speed servo control system is widely used in fields such as textile machinery, packaging machinery, printing machinery, etc.
(3) Force servo control system: mainly used to apply precise force or pressure. By measuring the applied force or pressure and comparing it with the set value, a force error signal is generated. The controller adjusts the output of the actuator based on the error signal to achieve the expected level of applied force or pressure. The force servo control system is widely used in fields such as assembly machinery and testing equipment.
(4) Torque servo control system: mainly used for precise control of the torque or torque of objects. By measuring the actual torque of an object and comparing it with the set value, a torque error signal is generated. The controller adjusts the output of the actuator based on the error signal to achieve the required torque control. The torque servo control system is widely used in fields such as automotive manufacturing and aerospace.
Classified by type of driving components
(1) Mechanical and Electrical Servo System: A servo control system primarily driven by servo motors. The electromechanical servo system has the characteristics of high precision, high stability, and fast response, and is widely used in various fields such as automation equipment and robots.
(2) Hydraulic servo system: a servo control system mainly driven by hydraulic cylinders. Hydraulic servo systems have the advantages of high power, strong load-bearing capacity, and good impact resistance, but their response speed is relatively slow, making them suitable for heavy-duty and large equipment.
(3) Pneumatic servo system: a servo control system mainly driven by cylinders. Pneumatic servo systems have the characteristics of simple structure, low cost, and easy maintenance, but their accuracy and stability are relatively low, making them suitable for situations where precision is not required.
Classified by control principles
(1) Open loop control servo system: a servo control system without feedback loop. The open-loop control servo system has a simple structure and low cost, but its accuracy and stability are poor, making it suitable for situations where precision is not required.
(2) Closed loop control servo system: a servo control system with feedback loop. The closed-loop control servo system monitors the motion status of the controlled object in real time through sensors, and feeds back this information to the controller for adjustment and control, thereby achieving high-precision and stable control effects. Closed loop control servo systems are widely used in various high-precision control scenarios.
4、 Working principle of servo control system
The working principle of servo control system can be summarized as the following steps:
Sensors monitor the real-time motion status of the controlled object (such as position, velocity, acceleration, etc.) and transmit this information to the controller.
The controller processes and calculates the received information based on preset control algorithms and instructions, generating control signals.
The control signal is converted into actual physical quantities (such as force, speed, position, etc.) through actuators (such as servo motors, hydraulic cylinders, etc.) to adjust and control the controlled object in real time.
The motion state of the controlled object is monitored in real-time by sensors and fed back to the controller, forming a closed-loop control process. By continuously monitoring, adjusting, and controlling, precise control of the motion state of the controlled object can be achieved.
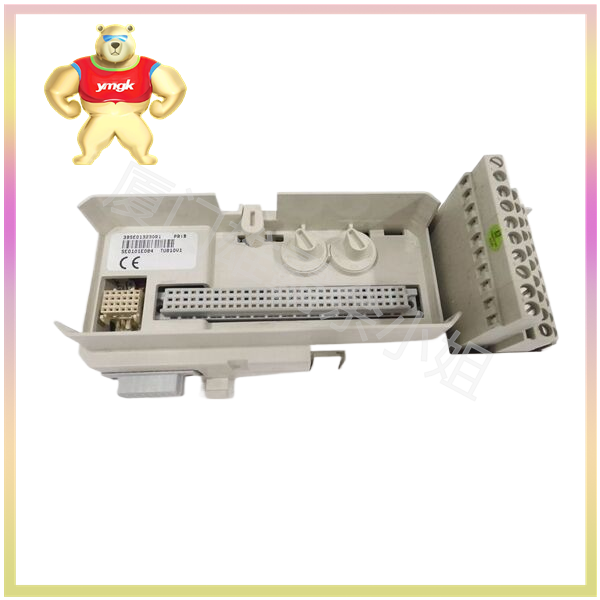
5、 Application Fields of Servo Control Systems
Servo control systems are widely used in various industrial equipment, precision instruments, and robots, such as CNC machine tools, robots, textile machinery, packaging machinery, printing machinery, assembly machinery, testing equipment, automotive manufacturing, aerospace, etc. In these fields, servo control systems play a crucial role in achieving efficient and precise control of production processes and product quality, driving the development of industrial automation and intelligence.
6、 Summary
As a core component of modern automation technology, servo control system has the characteristics of high precision, high stability, fast response, and easy programming. This article provides a detailed introduction to the definition, classification, working principle, and application fields of servo control systems. Through the explanation in this article, readers can comprehensively understand the relevant knowledge of servo control systems, providing reference and inspiration for future learning and work.