PLC is a widely used automation controller that can manage various automation processes through input and output control signals. The “analog” input/output and “digital” input/output of PLC are two common types of PLC, with significant differences between them.
The difference between PLC with analog input/output and PLC without analog input/output is that they can control and process different types of signals. Analog input/output and digital input/output are both types of signals used in control systems.
The “digital quantity” signal is represented by discrete states such as on and off, true and false, etc. This signal is binary, with only two possible states: ON and OFF. In the digital input/output module of PLC, these signals are processed into discrete values that can be used to control the status of switches, gates, motors, etc.
Analog signals are represented by continuous numerical values, such as voltage, current, pressure, temperature, etc. This signal is diverse and can have countless possible values. In the analog input/output module of PLC, these signals are processed into digital signals that can be used to control related equipment, such as regulating valves, controlling motor speed, and so on.
PLCs with analog input and output can handle a wider range of control signals because they have more input and output channels. These additional channels are essential for the flexibility of the control system.
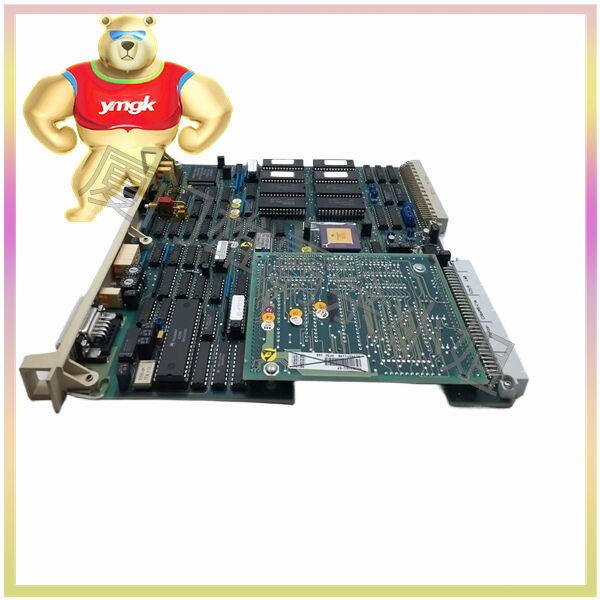
In addition, PLCs with analog input and output have several other advantages:
- Higher accuracy. PLCs with analog input and output typically have higher conversion accuracy and resolution, allowing for more accurate measurement and control of system parameters.
- A wider measurement range. As mentioned earlier, analog signals can represent a very wide range of numerical values. Therefore, PLCs with analog input and output can measure and control system parameters more widely.
- More flexible. PLCs with analog input/output can more easily adapt to different control scenarios. They can handle different types of sensors and actuators, and can be used in conjunction with other types of devices.
However, PLCs with analog input and output also have some limitations:
- The cost is relatively high. Due to the need for more hardware and channels to process analog signals, this type of PLC is typically more expensive than PLCs without analog inputs and outputs.
- More complex design and programming. PLCs with analog input and output require more complex hardware and software to manage and process signals, which may require higher design and programming skills.
- More difficult to repair. Due to its more hardware and channels, troubleshooting PLCs with analog input and output may be more difficult.
In short, whether choosing a PLC with analog output or without analog output, it is necessary to carefully consider the characteristics of the required automation control system. If you need to control multiple types of sensors and actuators, as well as a wider measurement range, choosing a PLC with analog output may be more suitable. Otherwise, choosing a PLC without analog output would be more cost-effective.