- Computational function
The operational functions of a simple programmable logic controller include logical operations, timing, and counting functions; The operation functions of ordinary programmable logic controllers also include data shifting, comparison, and other operation functions; More complex computational functions include algebraic operations, data transfer, etc; Large programmable logic controllers also have analog PID operations and other advanced computing functions. With the emergence of open systems, programmable logic controllers have communication functions. Some products have communication with lower level computers, some products have communication with same level or upper level computers, and some products also have data communication functions with factory or enterprise networks. When designing and selecting, one should start from the requirements of practical applications and choose the required computational functions reasonably. In most applications, only logical operations and timing counting functions are required. Some applications require data transmission and comparison. When used for analog detection and control, algebraic operations, numerical conversion, and PID operations are used. To display data, decoding and encoding operations are required. - Control function
The control functions include PID control operation, feedforward compensation control operation, ratio control operation, etc., which should be determined according to the control requirements. Programmable logic controllers are mainly used for sequential logic control. Therefore, in most cases, single loop or multi loop controllers are often used to solve analog control. Sometimes, dedicated intelligent input and output units are also used to complete the required control functions, improving the processing speed of programmable logic controllers and saving memory capacity. For example, using PID control units, high-speed counters, analog units with speed compensation, ASC code conversion units, etc.
- Communication function
Large and medium-sized programmable logic controller systems should support multiple fieldbus and standard communication protocols (such as TCP/IP), and should be able to connect with the factory management network (TCP/IP) when needed. The communication protocol should comply with ISO/IEEE communication standards and be an open communication network.
The communication interfaces of the programmable logic controller system should include serial and parallel communication interfaces, RIO communication interfaces, commonly used DCS interfaces, etc; The communication bus (including interface devices and cables) of large and medium-sized programmable logic controllers should be configured with 1:1 redundancy. The communication bus should comply with international standards, and the communication distance should meet the actual requirements of the device.
In the communication network of the programmable logic controller system, the communication rate of the higher-level network should be greater than 1Mbps, and the communication load should not exceed 60%. The main forms of communication networks for programmable logic controller systems are as follows:
1) A PC serves as the master station, and multiple programmable logic controllers of the same model serve as slave stations, forming a simple programmable logic controller network;
2) One programmable logic controller serves as the master station, while other programmable logic controllers of the same model serve as slave stations, forming a master-slave programmable logic controller network;
3) The programmable logic controller network is connected to a large DCS as a subnet through a specific network interface;
4) Dedicated Programmable Logic Controller Network (communication network for dedicated programmable logic controllers from various manufacturers).
To alleviate CPU communication tasks, communication processors with different communication functions (such as point-to-point and fieldbus) should be selected according to the actual needs of network composition.
- Programming function
Offline programming method: The programmable logic controller and programmer share a CPU. When the programmer is in programming mode, the CPU only provides services for the programmer and does not control the on-site devices. After completing the programming, the programmer switches to the running mode, and the CPU controls the on-site devices and cannot perform programming. Offline programming can reduce system costs, but it is inconvenient to use and debug. Online programming method: The CPU and programmer have their own CPUs. The host CPU is responsible for on-site control and exchanges data with the programmer during a scanning cycle. The programmer sends the online program or data to the host, and in the next scanning cycle, the host runs according to the newly received program. This method is costly, but easy to debug and operate, and is commonly used in large and medium-sized programmable logic controllers.
Five standardized programming languages: Sequential Function Diagram (SFC), Ladder Diagram (LD), Functional Block Diagram (FBD), three graphical languages, and Statement Table (IL) and Structured Text (ST), two textual languages. The selected programming language should comply with its standard (IEC6113123) and also support multiple programming forms such as C, Basic, etc. to meet the control requirements of special control situations.
- Diagnostic function
The diagnostic function of programmable logic controllers includes hardware and software diagnostics. Hardware diagnosis determines the location of hardware faults through logical judgment of hardware, while software diagnosis is divided into internal diagnosis and external diagnosis. Diagnosing the internal performance and functionality of a PLC through software is called internal diagnosis, while diagnosing the information exchange function between the CPU and external input/output components of a programmable logic controller through software is called external diagnosis.
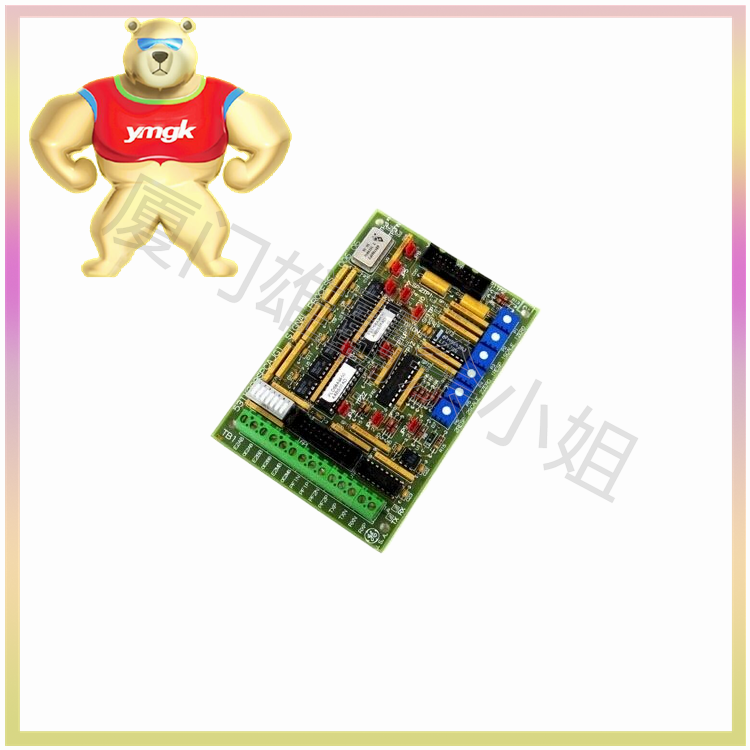
The strength of the diagnostic function of programmable logic controllers directly affects the technical requirements for operation and maintenance personnel, and affects the average repair time.
- Processing speed
The programmable logic controller operates in a scanning mode. From the perspective of real-time requirements, the faster the processing speed, the better. If the signal duration is less than the scanning time, the programmable logic controller will not be able to scan the signal, resulting in the loss of signal data.
The processing speed is related to the length of the user program, CPU processing speed, software quality, etc. The response and speed of programmable logic controller contacts are fast, and the execution time of each binary instruction is about 0.2-0.4Ls, making it suitable for applications with high control requirements and corresponding fast requirements. The scanning cycle (processor scanning cycle) should meet the following requirements: the scanning time of small programmable logic controllers should not exceed 0.5mS/K; The scanning time of large and medium-sized programmable logic controllers shall not exceed 0.2ms/K.
Controller type
Programmable logic controllers are divided into two types based on their structure: integral type and modular type. They are also divided into on-site installation and control room installation based on their application environment; Divided by CPU word length into 1-bit, 4-bit, 8-bit, 16 bit, 32-bit, 64 bit, etc. From an application perspective, the selection can usually be based on control functions or input/output points.
The I/O points of the integrated programmable logic controller are fixed, so the user’s choice is limited and it is used for small control systems; Modular programmable logic controllers provide a variety of I/O cards or cards, allowing users to choose and configure the number of I/O points for the control system in a reasonable manner. The function expansion is convenient and flexible, and it is generally used for large and medium-sized control systems.