The number of DCS control system points is usually provided by the design institute. The DCS system points are the total number of I/O points for the instrumentation profession, I/O points for the electrical profession, and communication points between the DCS system and other systems. Accurately counting the I/O points of electrical and instrumentation can avoid the problem of coordination inconsistency between the electrical and instrumentation specialties. Accurate DCS points can provide a basis for users to make decisions on DCS system brands and DCS system costs.
DCS systems usually involve automation control such as thermal detection, analog control, sequence control, and logic control. The number of DCS system points is calculated from five aspects: AI simulation input points, AO simulation output points, DI switch input points, DO switch output points, and DCS communication points with other systems. The following introduces the calculation methods for DCS system points in instrumentation and electrical specialties:
How to calculate the number of AI input points?
AI refers to entering the DCS system or
PLC
The analog input signal. The AI input signals that can be directly input into the DCS system from the site include thermocouples (J, K, T, N, E, R, S, and B scale thermocouples), thermal resistance signals (Cu50, Cu100, Pt100, and Pt50 scale thermocouples), standard current signals (4-20mA, 0-20mA), standard voltage signals (1-5V, 0-5V, and 0-10V), and pulse signals; If other forms of signals need to be sent to the DCS system, signal isolators, current transmitters, voltage transmitters and other signal conversion equipment should be used to convert the signal into 4-20mA or 1-5V before sending it to the DCS system.
① Thermocouple AI input point statistics
Calculate based on one AI point for a single assembled thermocouple or a single armored thermocouple; Double mounted assembled thermocouples or double armored thermocouples need to display the temperature of two sensors at the same measuring point in the DCS system, calculated as 2 AI points. Only one temperature at the measuring point should be displayed and calculated as 1 AI point; Single or multi-point thermocouples are commonly used to monitor the temperature of different parts of the same measuring point. If there are multiple measuring points, the AI input of the thermocouple is calculated based on the number of points.
② Statistics of input points for thermistor AI
The method for calculating the number of input points for thermistor AI is the same as that for thermocouple AI.
③ Standard current and voltage AI input point statistics
Calculate one AI point for each 4-20mA, 0-2mA, 0-5V, 1-5V, or 0-10V signal sent to the DCS system, and calculate the corresponding range of the input signal. Two line transmitters (including temperature transmitters, pressure transmitters, liquid level transmitters, flow transmitters, etc.) require DC24V power supply, so it is best to separately count the AI points to facilitate DCS system integration and wiring. Special note: Field instruments such as pressure gauges, bimetallic thermometers, and glass rotor flow meters displayed on site are not included in the DCS system point calculation.
How to calculate the number of AO output points?
AO refers to the analog output signal sent by the DCS system or PLC to control the on-site execution equipment. There are generally five types of AO outputs: 4-20mA, 0-20mA, 0-5V, 1-5V, and 0-10V. 4-20mA is the most commonly used DCS system AO output, which is usually connected to devices such as electric actuators, pneumatic actuators, frequency converters, power regulators, and industrial control modules. Usually, each controlled object corresponds to one AO output, and the number of AO output points is the same as the number of controlled devices.
How to calculate the number of DI input points?
DI refers to the switch input signal that enters the DCS system or PLC. The DI input must be a passive contact, TTL or CMOS level signal. After entering the DCS system or PLC, DI often connects to DC24V or DC48V to query the voltage.
The DI input for instrumentation usually comes from the alarm contacts of on-site electric contact pressure gauges, electric contact bimetallic thermometers, electric contact water level gauges, liquid level switches, flow switches, flame detection, electric contact water level gauges, and other instruments. Each alarm contact is calculated as a point DI input when connected to the DCS system. The calculation of DI points in electrical engineering is quite complex, which will be specifically introduced later in the article.
How to calculate the number of DO output points?
DO refers to the switch output signal sent by DCS system or PLC to control on-site equipment, usually connected to other electrical equipment of different voltage levels through intermediate relays. The DO output in instrumentation is commonly used to control external indicator lights, solenoid valves, sound and light alarms, electrical controls, multi turn electric actuators, contactors, and other equipment. The number of DO output points required for DCS system control of different devices varies. The following are common I/O points for controlled objects: ① Switch type electric actuators: each actuator valve position feedback 4-20mA calculation AI input 1 point, valve forward/reverse control calculation DO output 2 points, valve open/close position signal calculation DI input 2 points, valve open/close torque fault signal calculation DI input 2 points. ② Switch type multi turn electric actuator (AC380V power supply): Each actuator valve position feedback 4-20mA calculates AI input 1 point (if there is no feedback signal, this AI point is not calculated), valve forward/reverse control calculates DO output 2 points, valve fully open/closed (limit open/close) calculates DI input 2 points, actuator over torque/over torque fault signal calculates DI input 2 points Adjustable electric actuator: Each actuator valve position feedback calculates 1 AI input point, valve control signal calculates 1 AO output point, and actuator fault alarm signal calculates 1 AI input point (fault alarms are common in intelligent electric actuators, and AI points are not calculated if there is no fault alarm signal) Adjustable multi turn electric actuator: Each actuator valve position feedback calculates 1 AI input point, the actuator 4-20mA control signal calculates 1 AO output point, the ESD emergency control signal calculates 1 DO output point (ESD emergency control signal is common in intelligent multi turn electric actuators, if this function is not available, the DO point is not calculated), and the on/off torque alarm signal calculates 2 DI input points. ⑤ Inverter: Each inverter calculates 1 AI input point for frequency feedback, 1 AO output point for frequency given signal, 1 DO output point for running/stopping given command, 1 DI input point for inverter fault alarm calculation, 1 DO output point for fault reset calculation, and 1 DI input point for inverter operation status calculation.
If the frequency converter and communication method are connected to the DCS system, only one communication point needs to be calculated, and no other points need to be calculated.
How do electrical majors calculate points?
① DCS system points for conventional electrical control
The simplest
electric machinery
The control circuit requires 2 DI inputs and 1 DO output. Calculate one DI input point for each circuit operating status (from the auxiliary contact of the contactor), one DO output point for the start/stop control signal (connected to the contactor coil), and one DI input point for the fault signal (from the overload signal of the thermal relay or motor protector). If the motor circuit requires current display and local/remote control, in addition to calculating 2 DI and 1 DO, the current signal (from the current transmitter) should be calculated with 0-3 AI input points (low-power motors usually do not need to monitor current, so this AI input point is not calculated; high-power three-phase motors need to calculate several AI input points if there are several phase currents that need to be sent to DCS display, and each 0-5A current signal must be converted into a 4-20mA signal through the current transmitter and sent to DCS, with a maximum of 3 points); If the motor needs to be controlled in multiple locations, the control location selection switch calculates one DI input.
Function description of motor control secondary circuit: The stop button on the electrical cabinet and on-site operation box can stop the motor from running in any state; The control location selection switch can select “local cabinet control”, “on-site control”, and “DCS control”. The start button at the corresponding position of the selection switch can start the motor; The motor start/stop operation can only be performed on the DCS system when the selection switch is in “DCS control”.
Electrical component description: 1SS in the secondary schematic diagram is the stop button on the electrical cabinet, and 1SS1 is the stop button on the on-site operation box; 1SB is the start button on the electrical cabinet, and 1SB1 is the start button on the on-site operation box; DO is the start/stop control output contact of DCS system; 1HR5 is the power indicator light; 1HR is the operation indicator light on the electrical cabinet, and 1HR1 is the operation indicator light on the on-site operation box; 1HG is the stop indicator light on the electrical cabinet, and 1HR1 is the stop indicator light on the on-site operation box; 1KK is the switch for operating the ground switch; 1KH is a thermal relay; 1km is the contactor; 1KA is the intermediate relay; 1FU is the secondary circuit insurance. ② The DCS system for voltage reduction starting electrical control calculates one DI input point for each voltage reduction starting circuit motor full voltage operation status signal (from the main contactor 1KM1 auxiliary contact), one DO output point for DCS start/stop control signal (connected to the contactor coil), one DI input point for electrical fault signal (from thermal relay or motor protector overload signal), and three AI input points for motor current signal (from three-phase current transmitter) (motor A, B, C phase current transmitter); If the motor needs to be controlled from multiple locations, select the switch state for the control location (when DCS system control is selected) and calculate one DI input point.
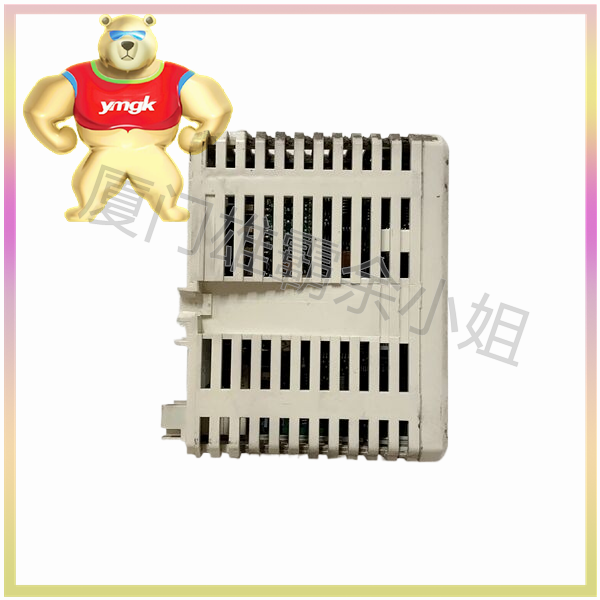
③ The DCS system controlled by the frequency converter calculates one DI input point for each frequency converter operating status signal (from the intermediate relay contact), one DO output point for the DCS system start/stop control signal (connected to the intermediate relay coil), one DI input point for the frequency converter fault signal (from the frequency converter), one DO output point for the fault reset calculation, and one AI input point for the frequency conversion feedback signal; Calculate one point of AO output based on the given frequency conversion signal. ④ The DCS system for motor forward and reverse control calculates the forward and reverse operating states of the motor (from the auxiliary contacts of the contactor) with 2 points for D1 input, 2 points for DI input of the forward/reverse fault signal (from the thermal relay), 2 points for DO output of the forward/reverse control (connected to the contact coil), and a maximum of 3 points for AI input of the motor current feedback signal (excluding current feedback) The DCS system is compatible with PLC functions, and the complex logic control calculates the I/O points of the DCS system according to actual engineering requirements (the calculation method is the same as that of calculating PLC points), which will not be listed and explained one by one here. The above DCS system point calculation method can quickly calculate the actual required DCS system hardware points. The actual configuration of the DCS system also needs to consider DCS system redundancy, usually increasing the redundancy by 20% according to the actual DCS system I/O points required by the user