What is a motion controller
A motion controller is a specialized controller that controls the operation mode of an electric motor. For example, the electric motor drives an object up to a specified position and then down by controlling the AC contactor through a travel switch, or uses a time relay to control the motor’s forward and reverse rotation or to stop and then stop again. The application of motion control in the fields of robots and CNC machines is more complex than in specialized machines, as the latter have simpler motion forms and are commonly referred to as General Motion Control (GMC).
Characteristics of motion controller
(1) The hardware composition is simple. Simply insert the motion controller into the PC bus and connect the signal lines to form the system;
(2) You can use the rich software already available on the PC for development;
(3) The code universality and portability of motion control software are good;
(4) There are many engineering personnel who can carry out development work, and there is no need for too much training to proceed with development.
Control form of motion controller
Point motion control: It only requires the endpoint position and is independent of the intermediate process of motion, that is, the motion trajectory. The corresponding motion controller requires fast positioning speed, and different acceleration and deceleration control strategies are adopted in the acceleration and deceleration stages of the motion.
During acceleration, in order to quickly accelerate the system to the set speed, the system gain is often increased and the acceleration is increased. In the final stage of deceleration, an S-shaped deceleration control strategy is adopted. In order to prevent vibration after the system is in place, the gain of the system will be appropriately reduced after planning is in place. Therefore, point motion controllers often have the ability to adjust control parameters and acceleration/deceleration curves online.
Continuous trajectory motion control: This control, also known as contour control, is mainly applied in the motion contour control of traditional CNC systems and cutting systems. The corresponding problem that the motion controller needs to solve is how to ensure the contour accuracy of the system during high-speed motion, while also ensuring a constant tangential velocity of the tool when moving along the contour. When processing small line segments, there is a multi segment program preprocessing function.
Synchronous motion control: refers to the coordinated control of motion between multiple axes, which can be achieved by synchronizing multiple axes throughout the entire motion or by locally synchronizing speed during the motion process. It is mainly used in system control that requires electronic gearbox and electronic cam functions. There are industries such as printing and dyeing, printing, papermaking, steel rolling, and synchronous shearing in the industry. The control algorithm of the corresponding motion controller often adopts adaptive feedforward control, which automatically adjusts the amplitude and phase of the control variable to ensure that a control effect equal to the interference amplitude and opposite in phase is added at the input end to suppress periodic interference and ensure synchronous control of the system.
What is PLC
Programmable logic controller is a digital operational electronic system specifically designed for use in industrial environments. It uses a programmable memory to store instructions for performing logical operations, sequential control, timing, counting, and arithmetic operations internally, and controls various types of mechanical equipment or production processes through digital or analog input and output.
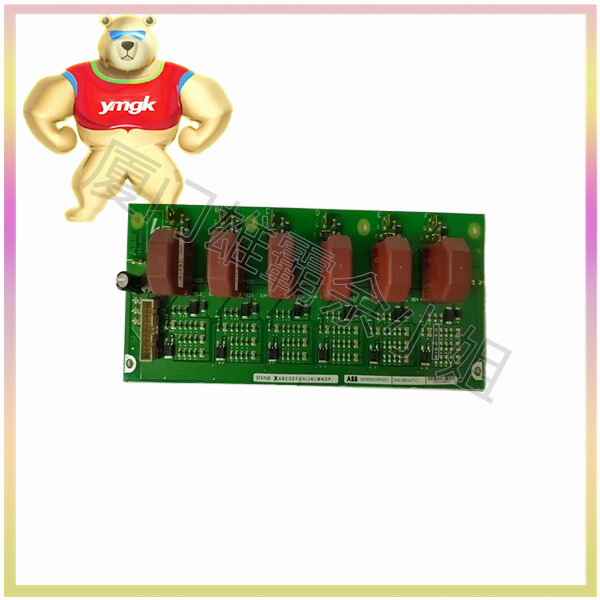
Characteristics of PLC
(1) High reliability. Due to the use of single-chip microcomputers in most PLCs, the integration level is high, coupled with corresponding protection circuits and self diagnostic functions, which improves the reliability of the system.
(2) Programming is easy. PLC programming often uses relay control ladder diagrams and command statements, which are much fewer in number than microcomputer instructions. Except for medium and high-end PLCs, general small PLCs only have about 16 instructions. Due to its visual and simple appearance, ladder diagrams are easy to master, convenient to use, and even do not require computer expertise for programming.
(3) Flexible configuration. Due to the modular structure adopted by PLC, users only need to combine them easily to flexibly change the functions and scale of the control system, making it applicable to any control system.
(4) The input/output function modules are complete. One of the biggest advantages of PLC is that it has corresponding templates for different field signals (such as DC or AC, switch values, digital or analog values, voltage or current, etc.), which can be directly connected to industrial devices (such as buttons, switches, sensing current transmitters, motor starters or control valves, etc.) and connected to the CPU motherboard through a bus.
(5) Easy to install. Compared with computer systems, the installation of PLC does not require a dedicated computer room or strict shielding measures. When in use, simply connect the detection device to the I/O interface terminals of the actuator and PLC correctly, and it can work normally.
(6) Fast running speed. Due to the fact that PLC control is executed by program control, its reliability and operating speed cannot be compared to relay logic control. In recent years, the use of microprocessors, especially with the widespread adoption of microcontrollers, has greatly enhanced the capabilities of PLCs and made the difference between PLCs and microcomputer control systems smaller and smaller, especially for high-end PLCs.
The difference between motion controller and PLC
Motion control mainly involves the control of stepper motors and servo motors, and the control structure mode is generally: control device+driver+(stepper or servo) motor.
The control device can be a PLC system or a dedicated automation device (such as a motion controller or motion control card). When a PLC system is used as a control device, although it has the flexibility and certain universality of a PLC system, it is difficult to achieve or program for high precision requirements such as interpolation control and sensitivity, and the cost may be high.
With the advancement and accumulation of technology, motion controllers have emerged, which solidify some universal and special motion control functions, such as interpolation instructions. Users only need to configure and call these functional blocks or instructions, which reduces programming difficulty and has advantages in performance, cost, and other aspects.
It can also be understood as follows: the use of PLC is a common motion control device. A motion controller is a special type of PLC specifically designed for motion control.