In industrial control systems, the usage rate of PLC is increasing, and the functions that PLC can complete are also increasing and becoming more advanced. So, what are the digital input modules and digital output modules that make up the PLC system? What are the differences between them?
The composition of a PLC should include a CPU module and input/output modules. If other motion or communication functions need to be completed, motion and communication modules should also be added. Of course, necessary equipment power should also be included to form a complete PLC system. In actual engineering projects, we need to select modules according to the design requirements and choose different types of PLCs based on the size of the system.
Why is the PLC input module divided into switch module and analog module
The digital module and analog module are both signal points transmitted from external devices to the PLC. They both belong to the function of input modules and are commonly used modules in our PLC system. To understand their differences, let’s first understand what they do. Another alias for digital input module is switch quantity, which means on/off, 0 and 1. Digital input module is commonly used for external button switches and other devices, and the feedback of device operation also belongs to the switch quantity point and is integrated into the digital module.
The analog input module converts the process values and monitored physical process values during our production process into standard current or voltage signals through a transmitter, which are then input into our analog module. For example, it monitors temperature changes during the production process, ranging from 0-100 ℃, and then converts them into signal modes supported by the analog module through a conversion circuit, such as 4-20mA. In this way, the analog module processes and transmits them to the CPU for program control.
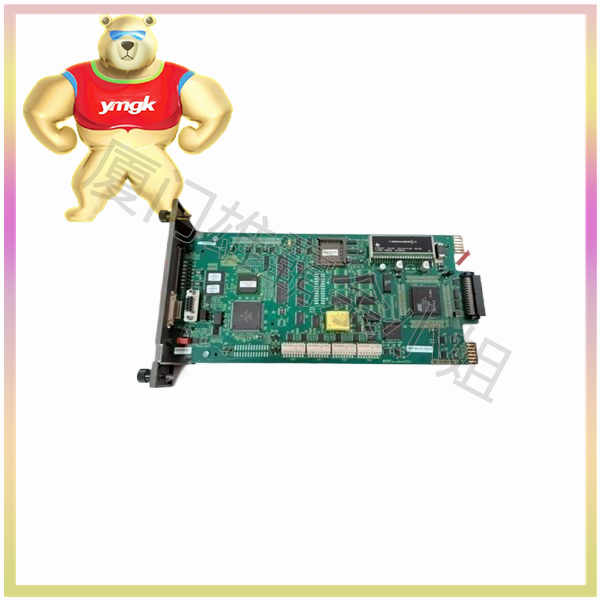