Distributed Control System (DCS) is a control system based on computer networks, which has high reliability, flexibility, and scalability. DCS is widely used for production process control in industries such as petroleum, chemical, power, metallurgy, and building materials.
1、 Composition of DCS
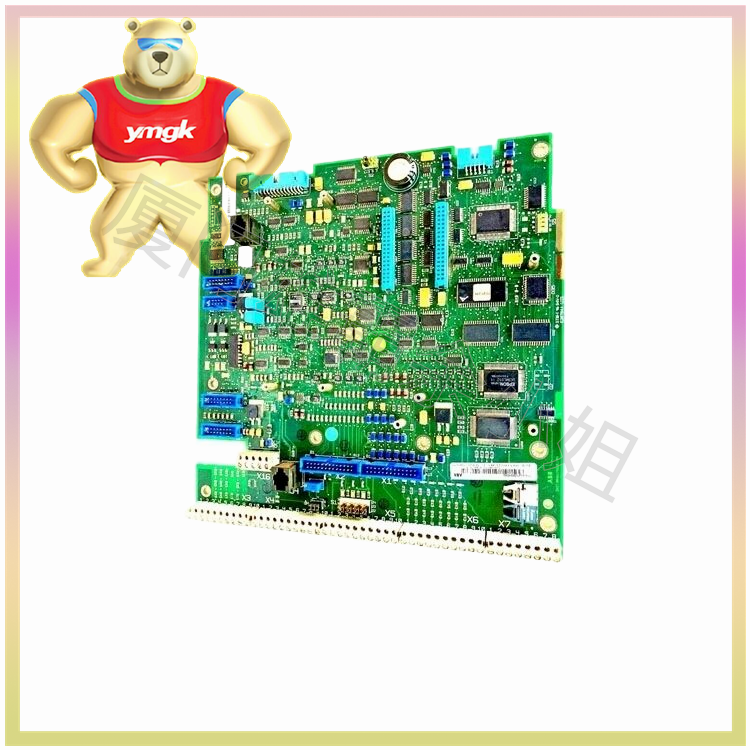
DCS mainly consists of the following parts:
Controller: The controller is the core component of DCS, responsible for real-time control of the production process. Controllers usually use high-performance microprocessors or digital signal processors, which have the characteristics of high speed, high precision, and high reliability.
I/O Module: The I/O module is the interface between DCS and field devices, responsible for converting the status signals of field devices into digital signals or converting the control signals of controllers into signals recognizable by field devices.
Communication Network: The communication network is the information transmission channel between various components of DCS, usually using communication technologies such as industrial Ethernet and fieldbus.
Human Machine Interface (HMI): The HMI is the interface through which operators interact with DCS, typically including operator stations, engineer stations, etc. The human-machine interface can display real-time data, trend curves, alarm information, etc. of the production process, and can also set and modify control parameters.
Database: The database is used to store DCS configuration information, historical data, alarm records, etc.
2、 The working principle of DCS
The working principle of DCS mainly includes the following aspects:
Data collection: DCS collects real-time status signals of on-site equipment, such as temperature, pressure, flow rate, etc., through input/output modules.
Data processing: The controller processes the collected data, such as filtering, scaling conversion, calculation, etc.
Control algorithm: The controller controls the processed data and generates control signals based on the control strategy and algorithm.
Control output: The controller outputs the generated control signal to the on-site equipment through the output/output module, achieving control over the production process.
Communication: DCS components exchange data and share information through a communication network.
Human computer interaction: Operators monitor and operate DCS through the human-machine interface.
Data storage: DCS stores real-time data, historical data, alarm records, etc. of the production process in a database for subsequent analysis and processing.
3、 Characteristics of DCS
Highly integrated: DCS integrates multiple functions such as control, communication, and human-computer interaction into one system, achieving comprehensive control and management of the production process.
High reliability: DCS adopts redundant design, fault detection and diagnosis technologies to ensure the stable operation of the system.
High flexibility: DCS can be modularized and expanded according to the needs of the production process, meeting the production requirements of different scales and complexities.
Highly Scalable: DCS can achieve system expansion by adding controllers, input/output modules, and other components.
High real-time performance: DCS adopts real-time operating system and high-speed communication technology to ensure the real-time transmission and processing of control signals.
Highly open: DCS supports multiple communication protocols and interfaces, allowing for integration and interoperability with other systems.
4、 Application of DCS
DCS is widely used in the following fields:
Petrochemical industry: DCS is used in the petrochemical industry to control production processes such as refining, fertilizers, and ethylene.
Power industry: DCS is used in the power industry to control the operation of equipment such as power plants and substations.
Metallurgical industry: DCS is used in the metallurgical industry to control the production processes of steel, non-ferrous metals, and other materials.
Building materials industry: DCS is used in the building materials industry to control the production processes of cement, glass, and other materials.
Water treatment industry: DCS is used in the water treatment industry to control the operation of equipment such as waterworks and sewage treatment plants.
Food and beverage industry: DCS is used in the food and beverage industry to control the production process, ensure product quality and safety.
5、 The development trend of DCS
With the continuous development of information technology, DCS is also constantly innovating and upgrading. The future DCS will have the following characteristics:
Higher intelligence: DCS will integrate technologies such as artificial intelligence and big data to achieve more intelligent control and management.
Stronger interconnection: DCS will realize deep integration with industrial Internet, Internet of Things and other technologies, and realize interconnection between equipment, systems and enterprises.
Better user experience: DCS will adopt a more user-friendly design, provide a more user-friendly human-computer interaction interface, and improve the work efficiency and satisfaction of operators.
Stronger security: DCS will strengthen security protection measures to prevent hacker attacks and data leaks, ensuring the safety and stability of the production process.
Lower energy consumption: DCS will adopt more energy-efficient technologies and equipment to reduce energy consumption in the production process and achieve green production.
In short, DCS, as an advanced control system, has been widely used in various fields. With the continuous development of technology, DCS will become more intelligent, interconnected, and user-friendly, providing more efficient, safe, and environmentally friendly solutions for the control and management of production processes.